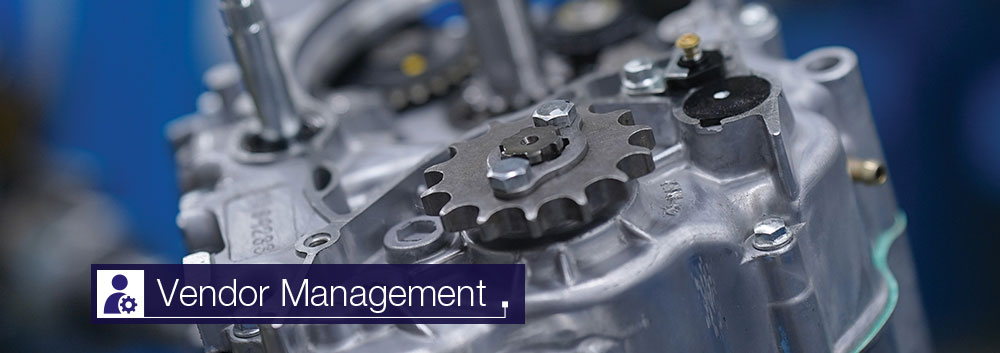
Vendor Management
Management Approach
Vendor interaction is a significant source of value development for the company. As a result, collaborating closely with them on matters such as sustainability is critical to achieving the Company’s long-term objectives. The Company’s supply chain comprises a large number of vendors, and it understands how difficult it is to meet sustainability requirements. Simultaneously, the Company sees tremendous potential in utilizing its knowledge and know-how to assist vendors in improving their performance.
The Company’s supply chain is based on the philosophy of 3As which are:
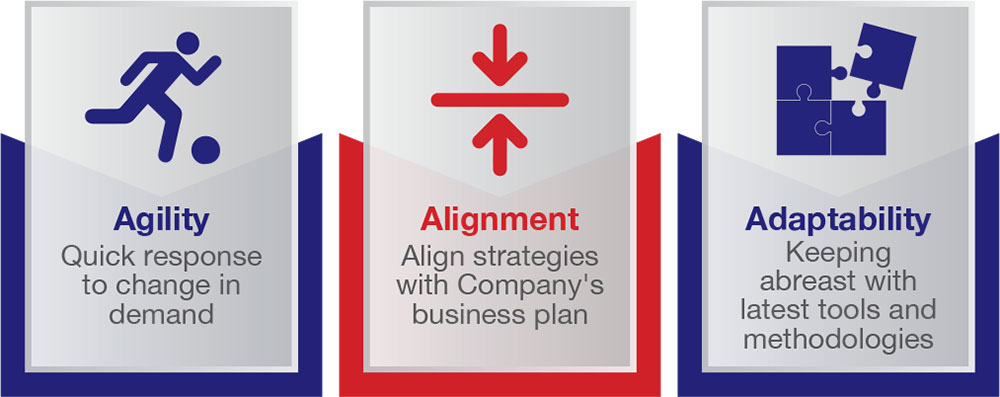
We strive for sustainable growth based on mutual trust with our vendors. We work openly and transparently as an equal partner with our vendors to build and maintain collaborative and competitive relationships that enable the implementation of best practices. Vendor-related policies are continually reviewed and analyzed in the light of industry best practices to ensure that
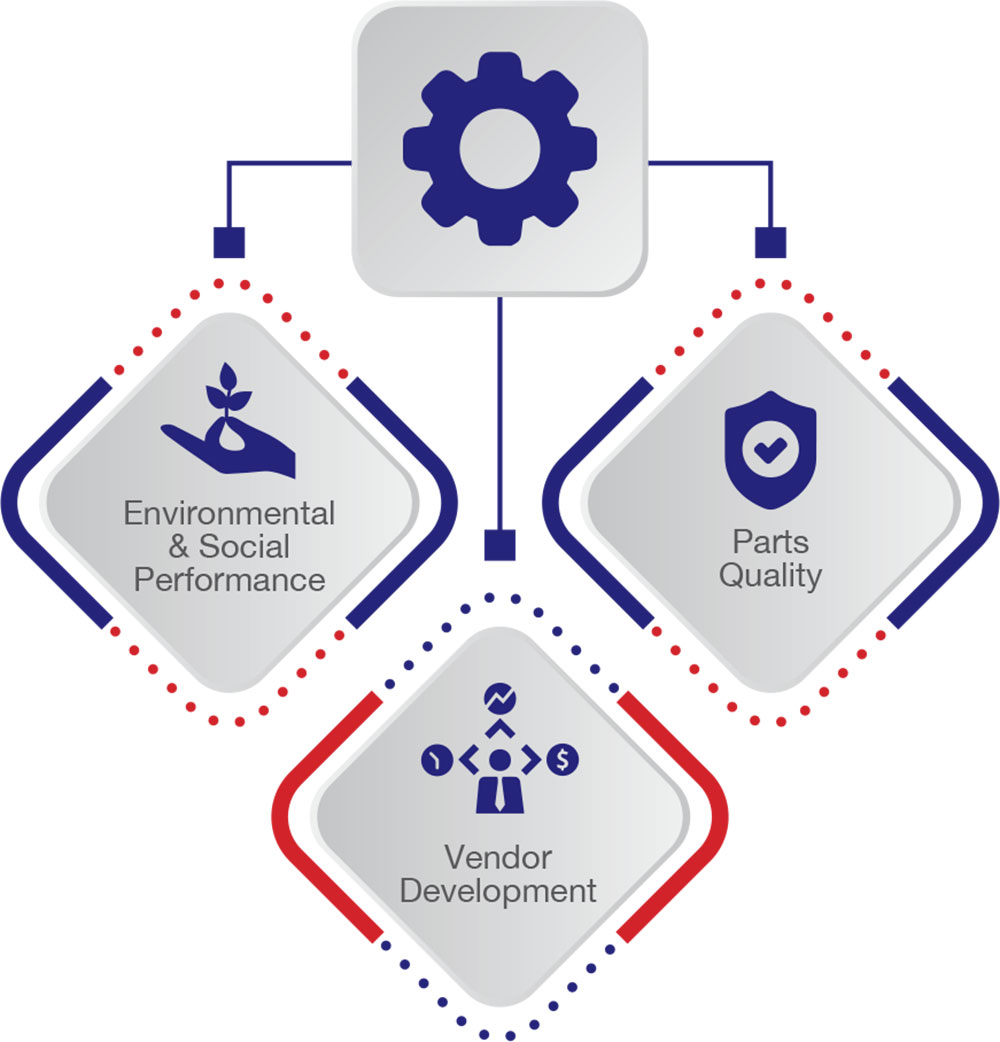
vendor’s meet the Company’s core focus areas i.e. parts quality, vendor development & social and environmental health and safety.
The Company’s relevant divisions, including Coordination & Planning, Procurement, Quality Assurance, and Logistics, are jointly responsible for guaranteeing long-term supply chain management. In order to maintain sustainability and ongoing progress, the Company focuses on controlling and mitigating vendor risks and maximizing vendor potential. To guarantee that the Company and its business partners are aware of local environmental, health, safety, and Labour laws, as well as legal obligations and worldwide sustainability principles, a variety of company-specific rules and policies have been established. These policies and guidelines allow the Company to go forward with its sustainability goals and ensure that they are met.
As far as it is qualitatively compatible, technically viable, and economically justified, the Company procures most of its essential materials from Pakistan, where its working facilities are located. Except for certain raw materials and parts that are not readily available in Pakistan, all raw materials and parts are sourced locally. However, it is ensured that all materials and parts are strictly aligned with Honda quality standards and are cost effective.
Vendor Induction and Communication
Vendor Selection
The Company’s vendor selection and approval procedure is based on a set of criteria that includes not only their capacity to deliver high-quality parts at reasonable rates, but also their commitment to environmental values. Decisions on sourcing are made in consultation with appropriate departments. The Company also seeks out and collaborates with businesses who have procurement and production standards that are similar to or identical to its own. All company’s vendors must recognize and sign the company’s Vendor Policy and Vendor CSR Guidelines.
In line with the Company’s selection criteria, all new vendors are screened and inducted only if they comply with sustainability principles detailed in ‘environmental and social performance’ section.
Vendor Diversity
A varied vendor base is an important aspect of the Company’s growth and success. It is crucial to deliver the promise of providing the best mobility solutions. The Company is dedicated to partnering with and growing businesses by providing opportunities and initiatives that help a wide range of vendors become viable and long-term businesses. To meet the demands and expectations of its consumers, the Company continues to cultivate beneficial ties with entrepreneurs from various backgrounds.
Business to Business Communication Portal
Establishing good and lasting relationships with the Company’s vendors requires open and transparent communication as well as fair and consistent behavior. The Company has made available various forums for engagement at different levels, including regional vendor meetings, business unit reviews, quarterly business update calls and participation in events organized by vendors and industry associations. Furthermore, a Business to Business link has been established, allowing the Company’s supply chain department and vendors to communicate with each other without delay. It has helped to achieve:
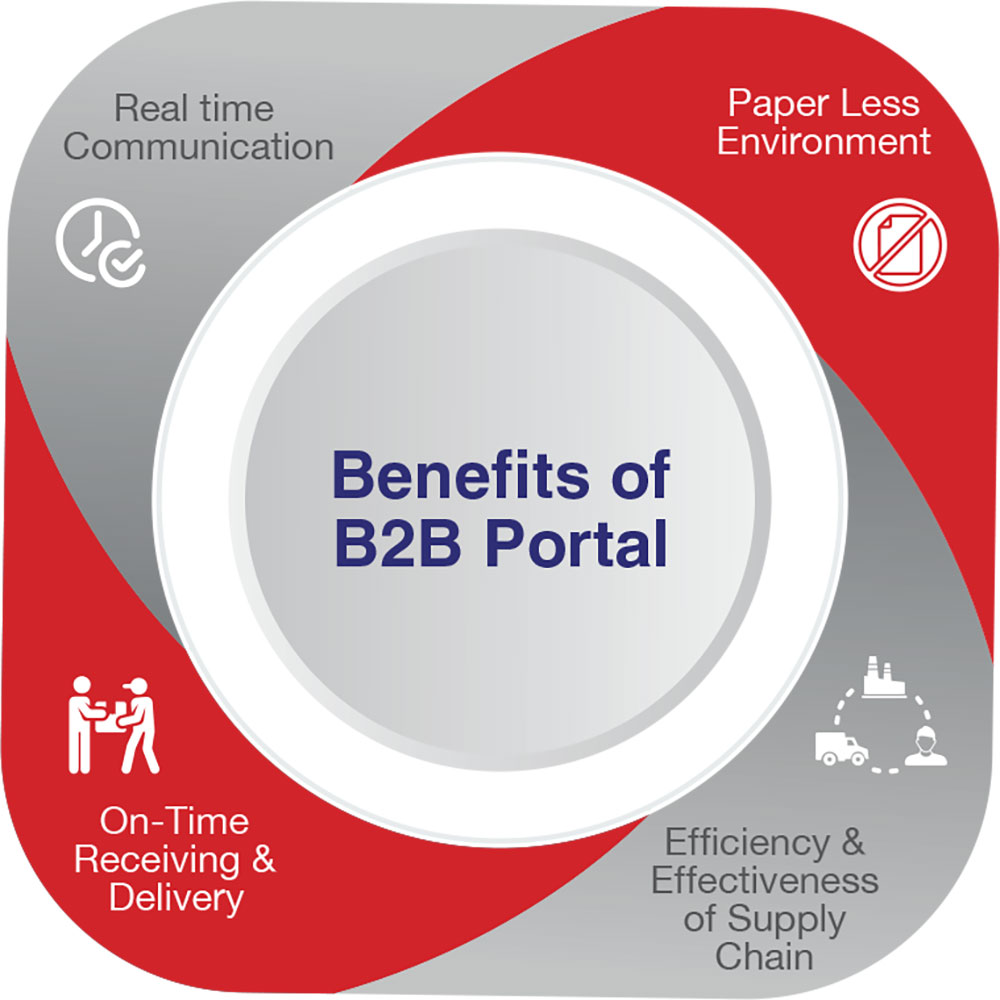
Parts Quality
The Company aims to keep its customers’ trust by emphasizing the importance of quality throughout its supply chain. To accomplish this, the Company requires its vendors to set up and operate a quality assurance system. In addition to the Company’s goal of sourcing inspection-free components, its vendors ensure that parts delivered through their manufacturing processes properly match the drawings and meet the 300 ppm rejection thresholds for incoming parts. To attain these quality goals, the following steps were taken:
Vendor Improvement Program (VIP)
Through numerous efforts, including the Company’s VIP program, which was introduced a few years ago, the Company aids its vendors in enhancing quality and operations. This program focuses on the six core areas listed below:
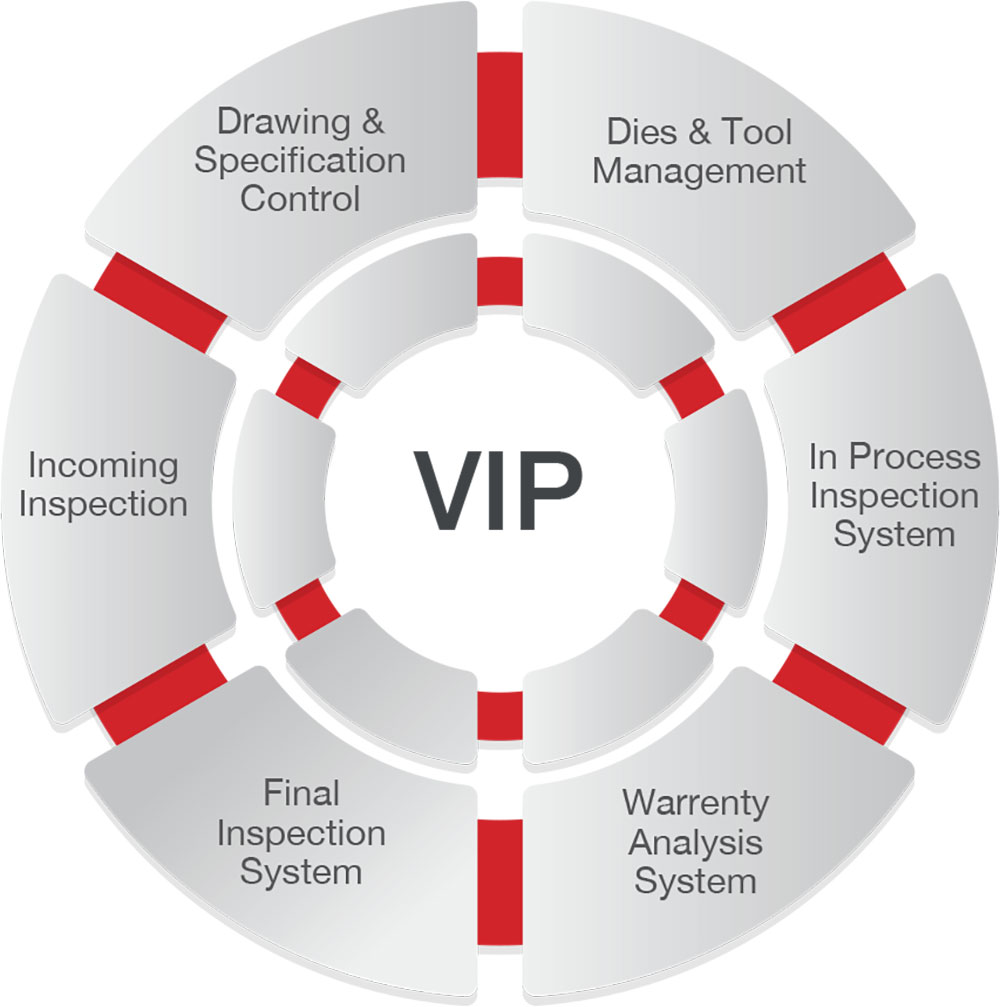
Certificates are awarded to vendors at the time of completion of the program. Further, they are reviewed and audited each year for recertification. Continuous follow up is carried out by VIP designated team which comprises of the Company’s employees from Supply Chain and Quality Assurance department. This year, 18 vendors were analyzed and assessed under this Program.
Vendor Development
The Company encourages its vendors to invest in their facilities, including boosting manufacturing capacity and implementing new technology. The goal is to keep the Company’s vendors well-equipped to satisfy business demands while also generating a good return on their investment.
On-site visits to our vendors assist in the identification of production bottlenecks and the formulation of process improvement strategies. We assure timely implementation of recommended actions through formal feedback and follow-up visits, resulting in improved engineering skills and job possibilities.
Environmental and Social Performance
The Company applies the same level of scrutiny to its vendors with regards to labor rights, human rights, and health, social and environmental requirements as it does to its own operations. The Company’s goal is to follow best practices and enable its vendors to replicate the same and be accountable for their sustainability performance.
Guidelines to Vendors
Corporate Social Responsibility is clearly and practically integrated into the Company’s day-to-day activities. All products and services are regularly assessed for their social and environmental impact. Given the rising demand for sustainability, the Company realizes the importance of sharing its sustainability strategy with its vendors. Vendors have been given the following guidelines in this regard. The Company believes that these guidelines help its vendors in maintaining a shared understanding of sustainability, to carry out initiatives proactively and to continue growing together.
- Create and maintain a social management system for the entire firm;
- Reduce GHG emissions to prevent climate change;
- Reduce waste disposal and transportation emissions by optimizing packaging and establishing efficient logistics operations.
- Prevent pollution and contamination of air, water, soil, etc;
- Enforce proper disposal of waste and implement optimum recycling of waste and disposals etc; and
- Compliance with laws and regulations along with commitment to protect human rights.
All vendors are monitored and evaluated against these principles on a continuous basis. During the year 38 vendors were evaluated for compliance and the Company has not found any major actual or potential negative impact of its supply chain or vendors on labour practices, human rights, or society that requires relationship termination.
Emission Reduction Caravan
In 2014, the Company launched an effort for its vendors called “Emissions Reduction Caravan.” Since then, the Company’s supply chain associates have been working closely with significant vendors to reduce their environmental footprint as part of this strategy. Process innovations that focus on production efficiency, energy conservation, material recycling, reuse, and CO2 emission reduction are given technical assistance. 38 vendors from both plants participated, contributing for 79% of total purchases, and the goal of reducing CO2 emissions by 1% was met.
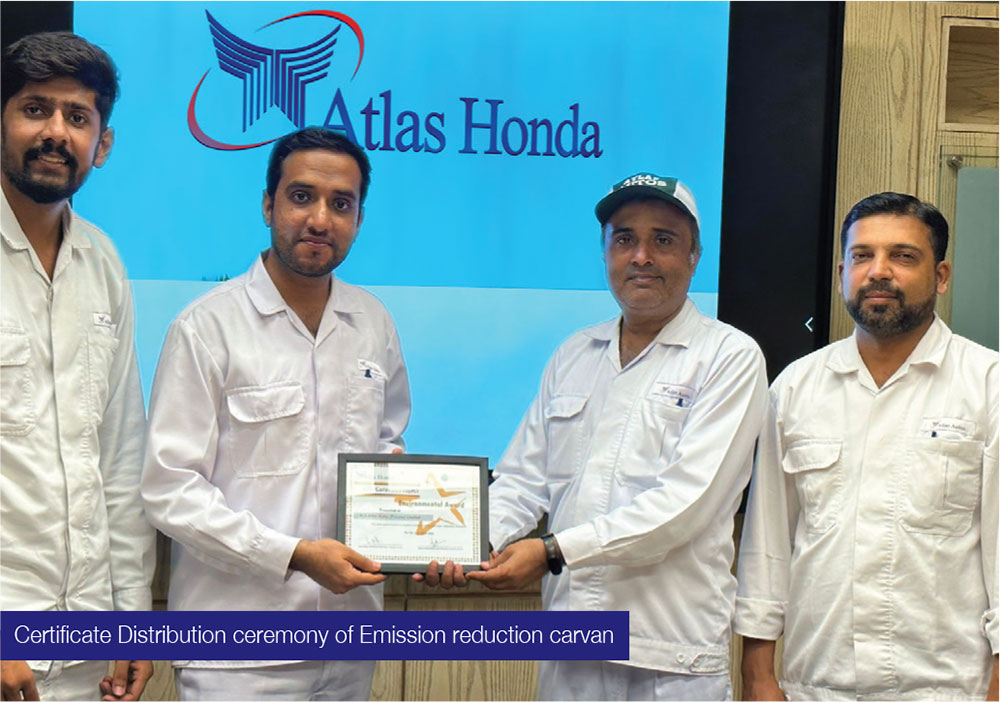
Logistics Operations
The Company’s supply chain operations oversee the delivery of parts and components from vendors to manufacturing facilities (“inbound”), while logistics operations oversee the transfer of finished motorcycles from the Company’s factories to dealerships (“outbound” freight). Designing and operating the transportation network, as well as creating high-quality and efficient packaging to safeguard products in transit, are all duties that are coordinated regionally. Freight emissions are influenced by a wide and complex range of inter-related factors, including the mode of transportation, the efficiency of the equipment used and the design of the freight network. The Company finds the most effective ways of achieving reductions through:
- Improving the design and operation of transportation networks
- Increasing vehicle utilization
- Increasing the use of more environmentally friendly means of transportation, such as the rail network
Environmental Impact Assessment Survey
Every year, the Company takes part in a Honda Motor Japan-developed environmental impact assessment survey. The following criteria were used to evaluate 36 vendors this year:
- Direct & Indirect GHG Emissions
- Green Purchasing Guideline
- Chemical Substance Management
- Environmental Management System
- Energy Conservation Guidelines
- Water Resources Guidelines
- Pollution Prevention Guidelines
- Biodiversity Guidelines
None of the selected vendors were identified as having any significant actual and potential negative environmental impacts.
Human Rights & Working Conditions
Respecting and protecting human rights – the fundamental and inalienable rights and freedoms to which all people are entitled – is at the core of the Company’s Labour practices. The Company strives to guarantee that everything it creates or has made for it complies with local laws and the Company’s commitment to human rights protection. To preserve employee rights, the Company has adopted strict requirements inside its operations and for vendors, as described in the following guidelines:
- Eliminate discrimination and ensure zero harassment at workplace in any aspect of employment based on race, ethnicity, nationality, religion, gender, or other characteristics;
- Avoid employment of workers who do not meet the legal minimum working age of each country and region;
- Avoid using forced Labour. Ensure that all Labour is voluntary and that employees have the freedom to leave their jobs;
- To comply with the laws & regulations regarding minimum wages, overtime, wage deductions, performance-based pay and other remuneration;
- To comply with the laws & regulations regarding the setting of employees’ working hours (including overtime) and granting of scheduled days off and paid annual vacation time etc; and
- Ensure a safe and healthy working environment for all associates.
Responsible Sourcing of Minerals
In procurement of certain raw materials, the Company has to comply with Dodd-Frank Act of United States which obligates companies to disclose the origin of certain raw materials to ensure that “conflict minerals”, such as tin, tungsten, tantalum and gold from the Democratic Republic of Congo or neighboring states, do not enter their products through their supply chain. The Company, therefore, monitors all vendors to make sure they do not source raw materials from the affected regions. Using a structured survey process and by working closely with vendors for increased supply chain transparency, the Company obtains confirmation that its vendors and their upstream vendors are obtaining material free from conflict minerals. Furthermore, the Company provides clear guidelines for vendors and raises awareness on conflict mineral related issues through education and support. The Company also collaborates with a cross-industry group called Conflict-Free Sourcing Initiative (CFSI) in this regard. In order to be confirmed as conflict free, the smelters and refiners are required to pass an independent third-party audit. The results from this year’s survey confirmed that our supply chain is based on conflict free sourcing.
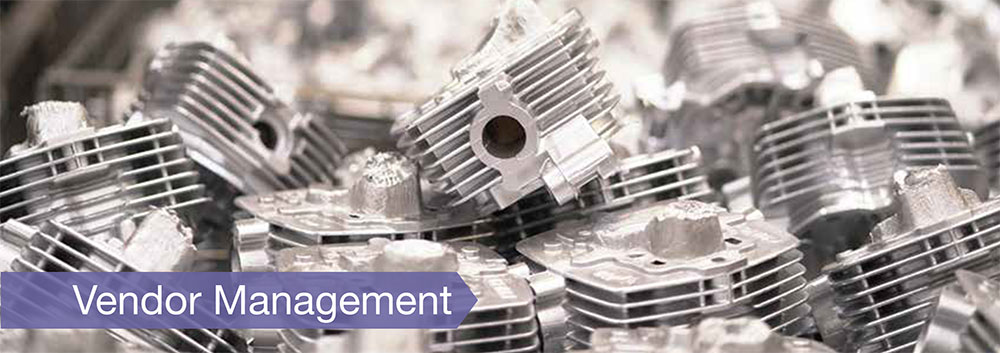
Vendor Management
Management Approach
Vendor interaction is a significant source of value development for the company. As a result, collaborating closely with them on matters such as sustainability is critical to achieving the Company’s long-term objectives. The Company’s supply chain comprises a large number of vendors, and it understands how difficult it is to meet sustainability requirements. Simultaneously, the Company sees tremendous potential in utilizing its knowledge and know-how to assist vendors in improving their performance.
The Company’s supply chain is based on the philosophy of 3As which are:
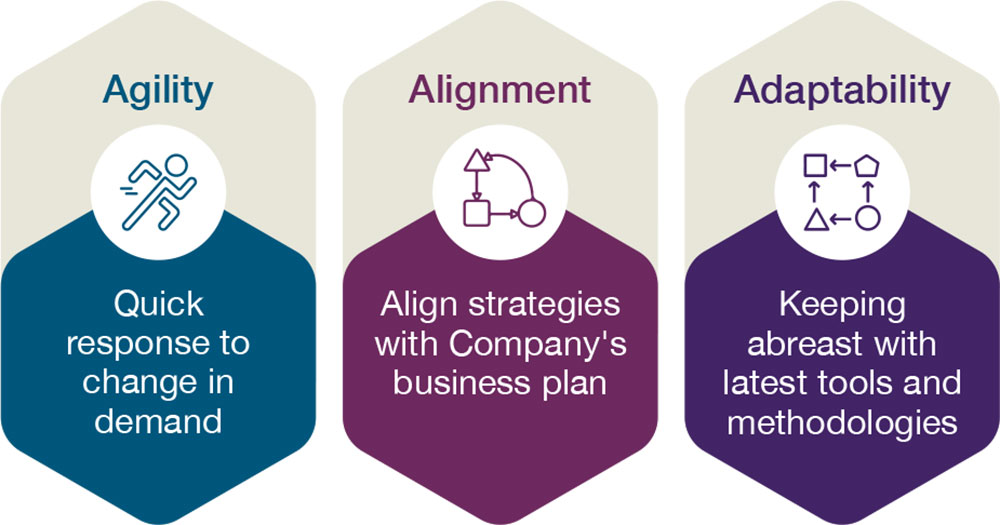
We strive for sustainable growth based on mutual trust with our vendors. We work openly and transparently as an equal partner with our vendors to build and maintain collaborative and competitive relationships that enable the implementation of best practices. Vendor-related policies are continually reviewed and analyzed in the light of industry best practices to ensure that vendor’s meet the Company’s core focus areas i.e. environmental & social performance, parts quality & vendor development.
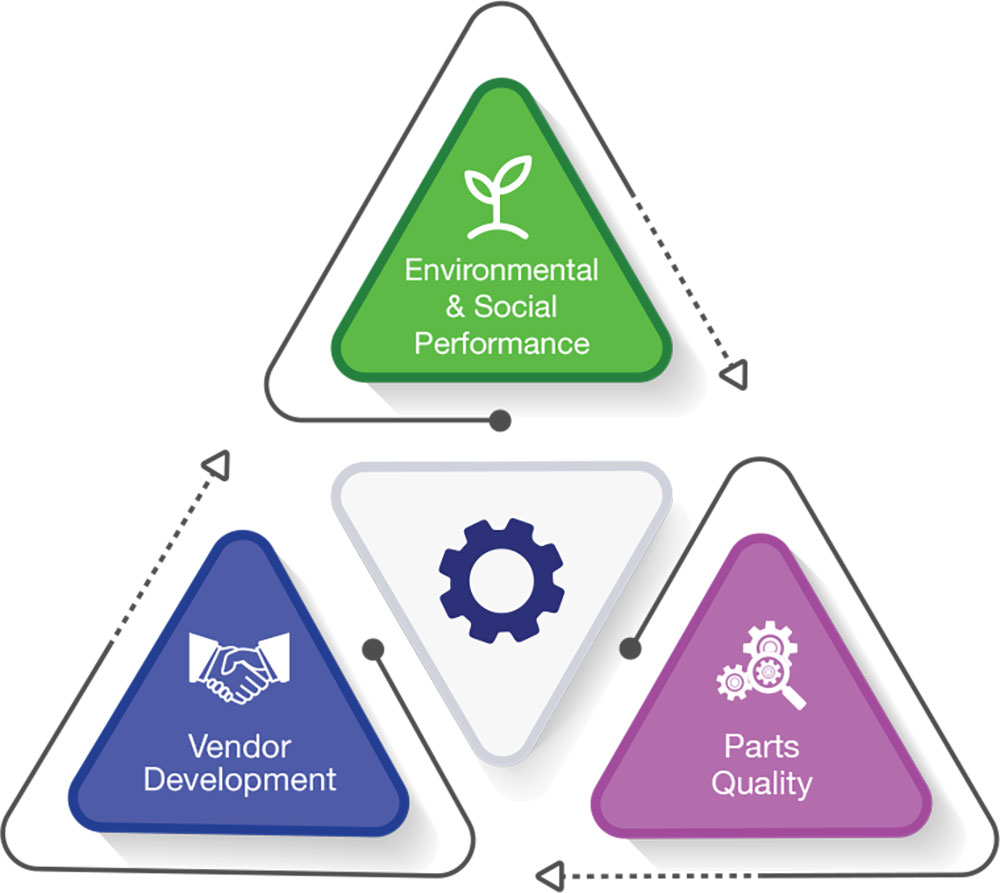
The Company’s relevant divisions, including Coordination & Planning, Procurement, Quality Assurance, and Logistics, are jointly responsible for guaranteeing long-term supply chain management. In order to maintain sustainability and ongoing progress, the Company focuses on controlling and mitigating vendor risks and maximizing vendor potential. To guarantee that the Company and its business partners are aware of local environmental, health, safety, and labour laws, as well as legal obligations and worldwide sustainability principles, a variety of company-specific rules and policies have been established. These policies and guidelines allow the Company to go forward with its sustainability goals and ensure that they are met.
As far as it is qualitatively compatible, technically viable, and economically justified, the Company procures most of its essential materials from Pakistan, where its working facilities are located. Except for certain raw materials and parts that are not readily available in Pakistan, all raw materials and parts are sourced locally. However, it is ensured that all materials and parts are strictly aligned with Honda quality standards and are cost effective.
Vendor Induction and Communication
Vendor Selection
The Company’s vendor selection and approval procedure is based on a set of criteria that includes not only their capacity to deliver high-quality parts at reasonable rates, but also their commitment to environmental values. Decisions on sourcing are made in consultation with appropriate departments. The Company also seeks out and collaborates with businesses who have procurement and production standards that are similar to or identical to its own. All company’s vendors must recognize and sign the company’s Vendor Policy and Vendor CSR Guidelines.
In line with the Company’s selection criteria, all new vendors are screened and inducted only if they comply with sustainability principles detailed in ‘environmental and social performance’ section.
Vendor Diversity
A varied vendor base is an important aspect of the Company’s growth and success. It is crucial to deliver the promise of providing the best mobility solutions. The Company is dedicated to partnering with and growing businesses by providing opportunities and initiatives that help a wide range of vendors become viable and long-term businesses. To meet the demands and expectations of its consumers, the Company continues to cultivate beneficial ties with entrepreneurs from various backgrounds.
Business to Business Communication Portal
Establishing good and lasting relationships with the Company’s vendors requires open and transparent communication as well as fair and consistent behavior. The Company has made available various forums for engagement at different levels, including regional vendor meetings, business unit reviews, quarterly business update calls and participation in events organized by vendors and industry associations. Furthermore, a Business to Business link has been established, allowing the Company’s supply chain department and vendors to communicate with each other without delay. It has helped to achieve:
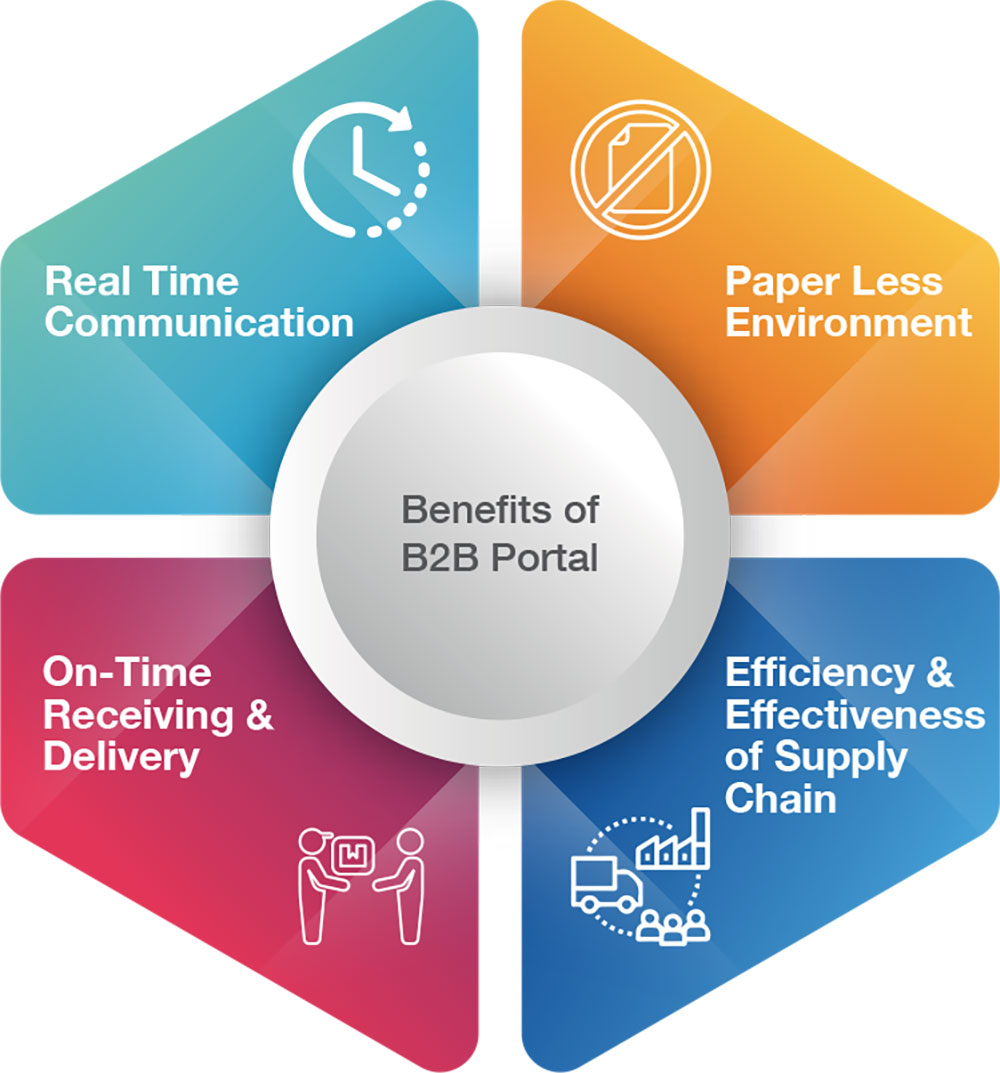
Parts Quality
The Company aims to keep its customers’ trust by emphasizing the importance of quality throughout its supply chain. To accomplish this, the Company requires its vendors to set up and operate a quality assurance system. In addition to the Company’s goal of sourcing inspection-free components, its vendors ensure that parts delivered through their manufacturing processes properly match the drawings and meet the 0.1 % rejection threshold for incoming parts. To attain these quality goals, the following steps were taken:
Vendor Improvement Program (VIP)
Through numerous efforts, including the Company’s VIP program, which was introduced a few years ago, the Company aids its vendors in enhancing quality and operations. This program focuses on the six core areas listed below:
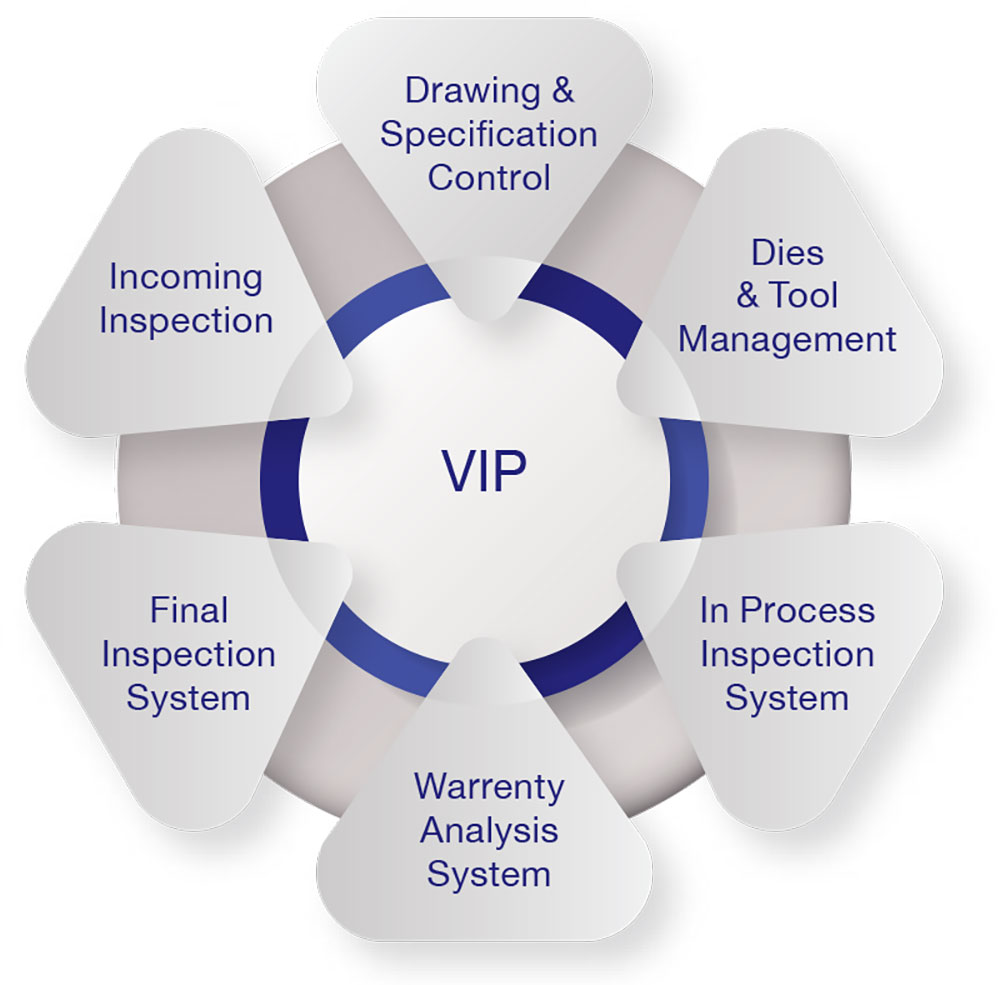
Certificates are awarded to vendors at the time of completion of the program. Further, they are reviewed and audited each year for recertification. Continuous follow up is carried out by VIP designated team which comprises of the Company’s employees from Supply Chain and Quality Assurance department. This year, 18 vendors were analyzed and assessed under this Program.
Vendor Development
The Company encourages its vendors to invest in their facilities, including boosting manufacturing capacity and implementing new technology. The goal is to keep the Company’s vendors well-equipped to satisfy business demands while also generating a good return on their investment.
On-site visits to our vendors assist in the identification of production bottlenecks and the formulation of process improvement strategies. We assure timely implementation of recommended actions through formal feedback and follow-up visits, resulting in improved engineering skills and job possibilities.
Environmental and Social Performance
The Company applies the same level of scrutiny to its vendors with regards to labor rights, human rights, and health, social and environmental requirements as it does to its own operations. The Company’s goal is to follow best practices and enable its vendors to replicate the same and be accountable for their sustainability performance.
Guidelines to Vendors
Corporate Social Responsibility is clearly and practically integrated into the Company’s day-to-day activities. All products and services are regularly assessed for their social and environmental impact. Given the rising demand for sustainability, the Company realizes the importance of sharing its sustainability strategy with its vendors. Vendors have been given the following guidelines in this regard. The Company believes that these guidelines help its vendors in maintaining a shared understanding of sustainability, to carry out initiatives proactively and to continue growing together.
- Create and maintain a social management system for the entire firm;
- Reduce GHG emissions to prevent climate change;
- Reduce waste disposal and transportation emissions by optimizing packaging and establishing efficient logistics operations.
- Prevent pollution and contamination of air, water, soil, etc;
- Enforce proper disposal of waste and implement optimum recycling of waste and disposals etc; and
- Compliance with laws and regulations along with commitment to protect human rights.
All vendors are monitored and evaluated against these principles on a continuous basis. During the year 36 vendors were evaluated for compliance and the Company has not found any major actual or potential negative impact of its supply chain or vendors on labour practices, human rights, or society that requires relationship termination.
Emission Reduction Caravan
In 2014, the Company launched an effort for its vendors called “Emissions Reduction Caravan.” Since then, the Company’s supply chain associates have been working closely with significant vendors to reduce their environmental footprint as part of this strategy. Process innovations that focus on production efficiency, energy conservation, material recycling, reuse, and CO2 emission reduction are given technical assistance. 36 vendors from both plants participated, contributing for 80% of total purchases, and the goal of reducing CO2 emissions by 1% was met.
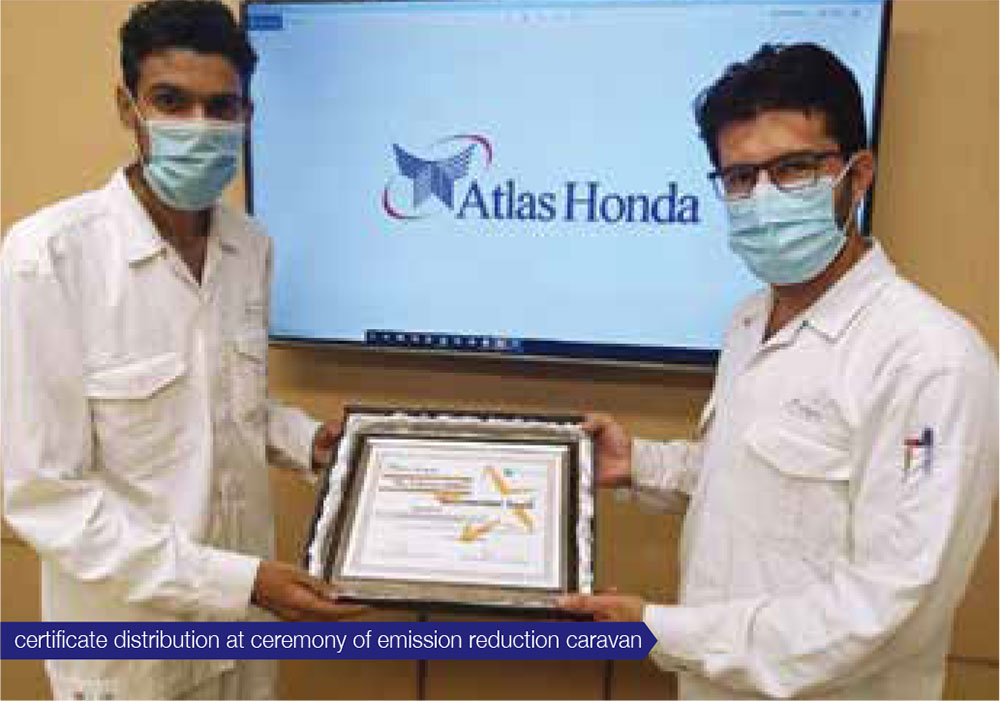
Logistics Operations
The Company’s supply chain operations oversee the delivery of parts and components from vendors to manufacturing facilities (“inbound”), while logistics operations oversee the transfer of finished motorcycles from the Company’s factories to dealerships (“outbound”). Designing and operating the transportation network, as well as creating high-quality and efficient packaging to safeguard products in transit, are all duties that are coordinated regionally. Freight emissions are influenced by a wide and complex range of inter-related factors, including the mode of transportation, the efficiency of the equipment used and the design of the freight network. The Company finds the most effective ways of achieving reductions through:
- Improving the design and operation of transportation networks
- Increasing vehicle utilization
- Increasing the use of more environmentally friendly means of transportation, such as the rail network
Environmental Impact Assessment Survey
Every year, the Company takes part in a Honda Motor Japan-developed environmental impact assessment survey. The following criteria were used to evaluate 36 vendors this year:
- Direct & Indirect GHG Emissions
- Green Purchasing Guideline
- Chemical Substance Management
- Environmental Management System
- Energy Conservation Guidelines
- Water Resources Guidelines
- Pollution Prevention Guidelines
- Biodiversity Guidelines
None of the selected vendors were identified as having any significant actual and potential negative environmental impacts.
Human Rights & Working Conditions
Respecting and protecting human rights – the fundamental and inalienable rights and freedoms to which all people are entitled – is at the core of the Company’s Labour practices. The Company strives to guarantee that everything it creates or has made for it complies with local laws and the Company’s commitment to human rights protection. To preserve employee rights, the Company has adopted strict requirements inside its operations and for vendors, as described in the following guidelines:
- Eliminate discrimination and ensure zero harassment at workplace in any aspect of employment based on race, ethnicity, nationality, religion, gender, or other characteristics;
- Avoid employment of workers who do not meet the legal minimum working age of each country and region;
- Avoid using forced labour. Ensure that all labour is voluntary and that employees have the freedom to leave their jobs;
- To comply with the laws & regulations regarding minimum wages, overtime, wage deductions, performance-based pay and other remuneration;
- To comply with the laws & regulations regarding the setting of employees’ working hours (including overtime) and granting of scheduled days off and paid annual vacation time etc; and
- Ensure a safe and healthy working environment for all associates.
Responsible Sourcing of Minerals
In procurement of certain raw materials, the Company has to comply with Dodd-Frank Act of United States which obligates companies to disclose the origin of certain raw materials to ensure that “conflict minerals”, such as tin, tungsten, tantalum and gold from the Democratic Republic of Congo or neighboring states, do not enter their products through their supply chain. The Company, therefore, monitors all vendors to make sure they do not source raw materials from the affected regions. Using a structured survey process and by working closely with vendors for increased supply chain transparency, the Company obtains confirmation that its vendors and their upstream vendors are obtaining material free from conflict minerals. Furthermore, the Company provides clear guidelines for vendors and raises awareness on conflict mineral related issues through education and support. The Company also collaborates with a cross-industry group called Conflict-Free Sourcing Initiative (CFSI) in this regard. In order to be confirmed as conflict free, the smelters and refiners are required to pass an independent third-party audit. The results from this year’s survey confirmed that our supply chain is based on conflict free sourcing.
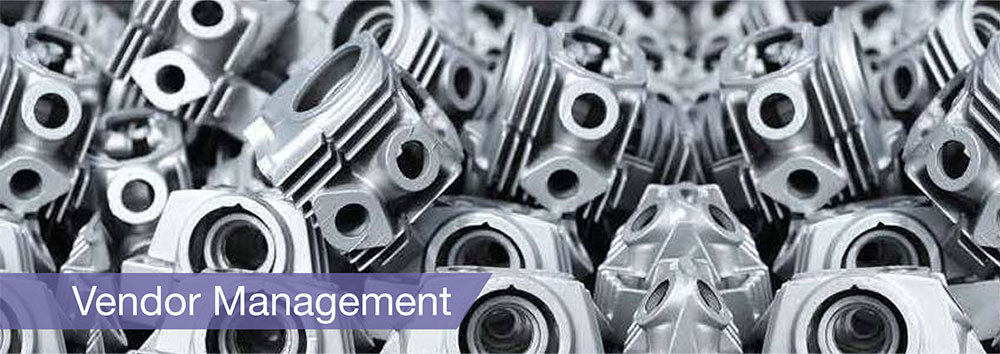
Vendor Management
Management Approach
The Company’s engagement with vendors is a major source of value creation. Therefore, working closely with them on issues, including sustainability is key for achievement of the Company’s long-term goals. The Company’s supply chain has a wide network of vendors and it recognizes the complexity of maintaining sustainability standards within it. At the same time, the Company sees great opportunities in leveraging its expertise and know-how to help vendors improve their performance.
The Company’s supply chain is based on the philosophy of 3As which are:
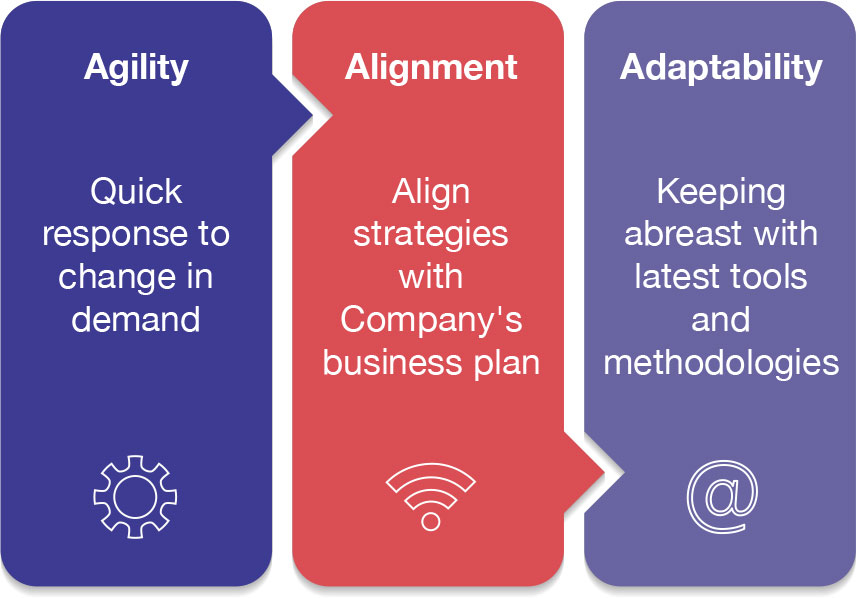
The Company aims to achieve sustainable growth built on a foundation of mutual trust with its vendors. We work in an open and transparent manner with our vendors as equal partners, developing and maintaining cooperative and competitive relations that enable us to implement best practices. During engagement with vendors, challenges and opportunities are discussed and in-depth analysis is carried out. Solutions to key issues are arrived at mutually. Policies relating to vendors are continuously reviewed and analysed with industry best practices to ensure our vendors meet the Company’s core focus areas i.e. parts quality, vendor development & social and environmental health and safety.
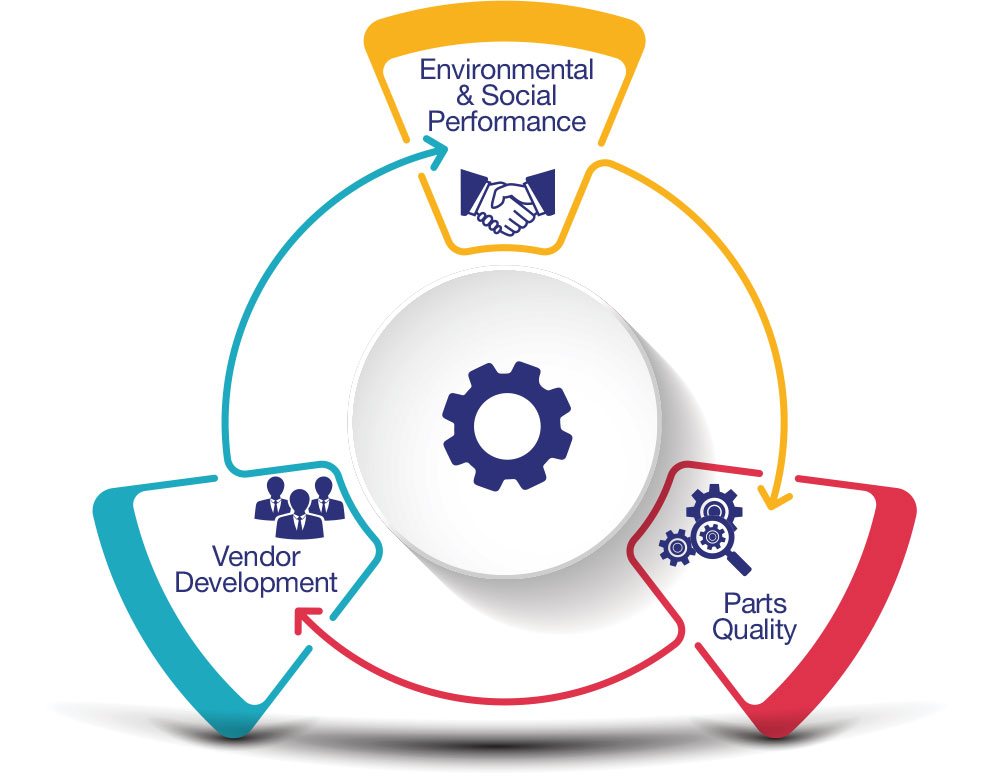
All relevant departments at the Company, including Coordination & Planning, Procurement, Quality Assurance and Logistics are jointly responsible for ensuring sustainable supply chain management. The Company’s focus is on managing and minimizing vendor risks and leveraging vendor potential, in order to ensure sustainability and continuous improvement. A number of company-specific guidelines and policies have been implemented to ensure that the Company and its business partners are aware of local environmental, health, safety, and labour laws, as well as legal requirements and international sustainability principles. These guidelines and policies enable the Company to drive forward the sustainability goals and ensure their compliance.
The Company procures most of its required materials from Pakistan i.e. where its operating facilities are located as far as the same is qualitatively compatible, technically feasible and economically justifiable. The raw materials and parts which are easily available in Pakistan are procured locally, except for those which are not available in Pakistan. However, it is ensured that all materials and parts are strictly aligned with Honda quality standards and are cost effective.
COVID-19 – Challenges for Supply Chain
COVID-19 pandemic transformed supply chain in its entirety as lockdowns were imposed globally to prevent the outbreak. Production halts, movement restrictions of people and goods, border closures, logistical constraints, as well as the slowdown of business activities were the fall-outs of the COVID-19 lockdown measures. In Pakistan, the economic activity was suspended during lockdowns and was subsequently allowed to resume work with strict SOPs directly impacting the availability of materials and components. Accordingly, the Company aligned its supply chain strategies to operate in compliance with government directives and ensured implementation of safety measures at vendors’ premises. These include restricting factory access to essential workers only, temperature screening at entry points, enhancing cleaning and sanitization protocols, implementing social distancing, working from home to reduce attendance and providing personal protective equipment where necessary.
Reacting to the effect of pandemic on the supply chain industry, participants across the value-chain have adopted efficient measures geared at sustaining production and delivery to final consumers. Some of these innovative measures include the use of technology to take up orders from customers, strategic partnerships between producers, intermediaries and delivery companies, innovative management of inventory to avoid stock-outs, etc. These alterations to supply chain methodologies have proved to be effective and have transformed future outlook of the function.
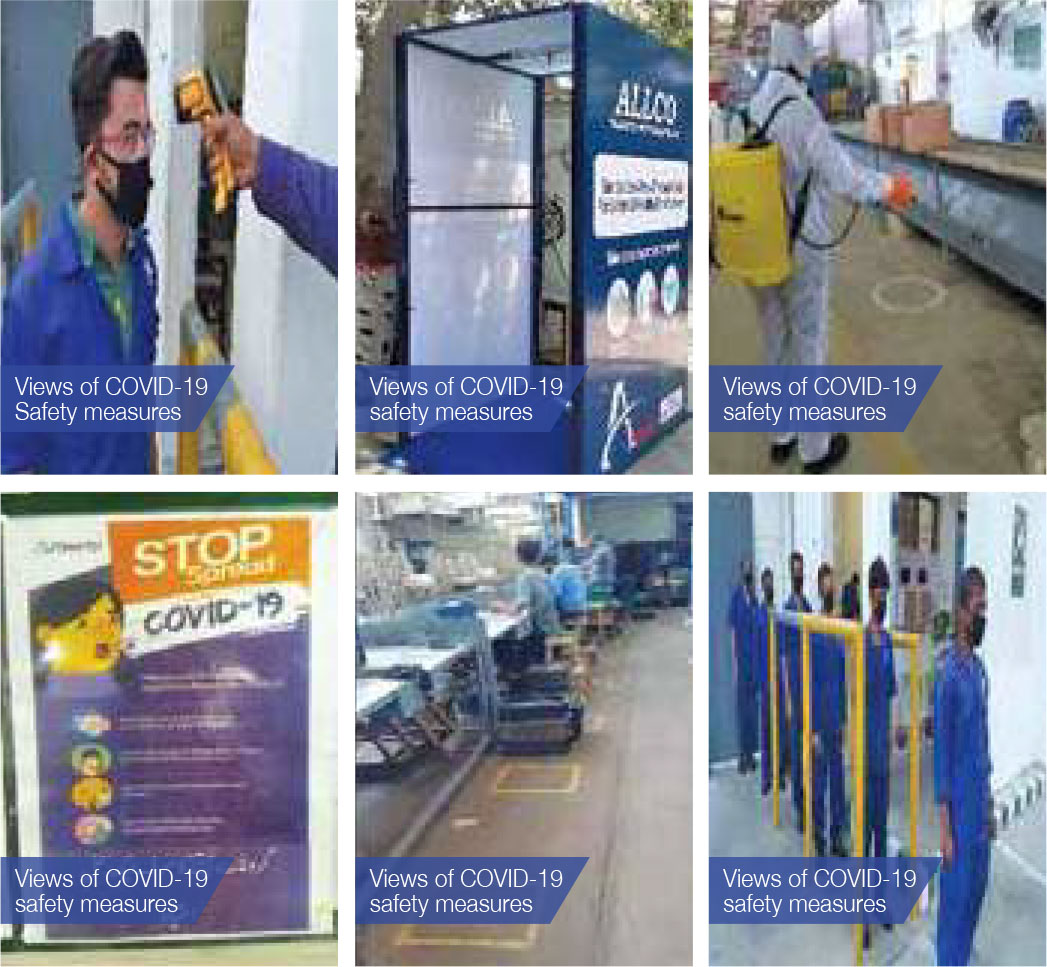
Vendor Induction and Communication
Vendor Selection
The Company’s vendor selection and approval process is based on a criteria comprising not only on their ability to provide quality parts at competitive terms but also their adherence to sustainability principles. Input for sourcing decisions is received from Supply Chain, Production, Coordination & Planning, Logistics and Finance departments. The Company also identifies and works with companies that have standards aligned or consistent with its own procurement and production practices. The Company also ensures that its Vendor Policy and Vendor CSR Guidelines are acknowledged and signed by all of its vendors.
In line with the Company’s selection criteria, all new vendors are screened and inducted only if they comply with sustainability principles detailed in ‘environmental and social performance’ section.
Vendor Diversity
The Company recognizes that a diverse supply base is an integral part of growth and success. It is crucial to deliver the promise of providing the best mobility solutions. The Company is committed to work with and developing businesses by creating opportunities and initiatives that enable diverse vendors to grow into profitable and sustainable enterprises. The Company continues to foster productive relationships with entrepreneurs from a wide range of backgrounds to meet its customers’ needs and expectations.
Business to Business Communication Portal
Open and transparent communication with fair and consistent behaviours is a key component in establishing strong and lasting relationships with the Company’s vendors. The Company has made available various forums for engagement at different levels, including regional vendor meetings, business unit reviews, quarterly business update calls and participation in events organized by vendors and industry associations. In addition, Business to Business link has been established which allows the Company’s supply chain department and vendors to communicate without delays. It has helped to achieve:

Further, this portal enables evaluation and appraisal of vendors on the basis of standardized quality and timely deliveries.
Parts Quality
The Company aims to keep its customers’ trust by emphasizing on importance of quality throughout its supply chain. To achieve this objective, the Company binds its vendors to establish and operate within a quality assurance system. Apart from the Company’s objective of procuring inspection free parts, its vendors validate that parts delivered through their manufacturing processes meet the drawings accurately and achieve target of 0.1% rejection for incoming parts. Following measures were taken to achieve these quality objectives:
Vendor Improvement Program (VIP)
The Company assists its vendors in improving quality and operations through various initiatives especially the Company’s VIP program launched few years ago. This program focuses on following six core areas:
- Drawing & Specification Control
- Dies & Tool Management
- In Process Inspection System
- Incoming Inspection
- Final Inspection System
- Warranty Analysis system
Certificates are awarded to vendors at the time of completion of the program. Further, they are reviewed and audited each year for recertification. Continuous follow up is carried out by VIP designated team which comprises of the Company’s employees from Supply Chain and Quality Assurance department. This year, 18 vendors were analysed and assessed under this program.
Vendor Development
The Company encourages its vendors to invest in their facilities including enhancing their manufacturing capacity and adapting new technology. The idea is to ensure that the Company’s vendors remain well-equipped to meet the demands of business while earning attractive returns on their investments.
The Company also believes in developing and strengthening competencies and skills of its vendors apart from their manufacturing capacities. For the purpose, the Company has been providing major technological assistance to its vendors, resulting in enhancement of their engineering skills and creation of employment opportunities. On-site visits to our vendors assist in identifying production bottlenecks and devising process improvements measures.
Environmental and Social Performance
The Company applies the same level of scrutiny to its suppliers with regards to labour rights, human rights, and health, social and environmental requirements as it does to its own operations. The Company’s goal is to follow best practices and enable its vendors to replicate the same and be accountable for their sustainability performance.
Guidelines to Vendors
Corporate Social Responsibility is embedded in the Company’s day to day operations in a clear and practical manner. All products and services are regularly monitored for their impact on society and the environment. Given the increased expectations regarding sustainability, the Company recognizes that it is essential to share its approach to sustainability with its vendors. In this regard, following guidelines have been issued to vendors. The Company believes that these guidelines help its vendors in maintaining a shared understanding of sustainability, to carry out initiatives proactively and to continue growing together.
- Establish and monitor a company-wide social management system;
- Prevent climate change via reducing GHG emissions;
- Optimize packaging and establish efficient logistics operations in order to reduce waste disposal and transport emissions;
- Prevent pollution and contamination of air, water, soil, etc.;
- Enforce proper disposal of waste and implement optimum recycling of waste and disposals etc.; and
- Compliance with laws and regulations along with commitment to protect human rights.
All vendors are monitored and evaluated against these guidelines and based on such evaluation, the Company has not come across any significant actual or potential negative impact of its supply chain or vendors’ on labour practices, human rights and society requiring termination of relationship.
Emission Reduction Caravan
In 2014, the Company undertook an initiative called ‘Emissions Reduction Caravan’ for its vendors. Since then, under this initiative, the Company’s supply chain associates are working in close coordination with major vendors to reduce their environmental footprint. Technical guidance is being provided for process improvements focused on production efficiency, energy conservation, material recycling, reuse and reduction in CO2 emission. 34 vendors from both plants, covering 77% of total purchases have participated and achieved the target of reduction in CO2 emission by 1%.
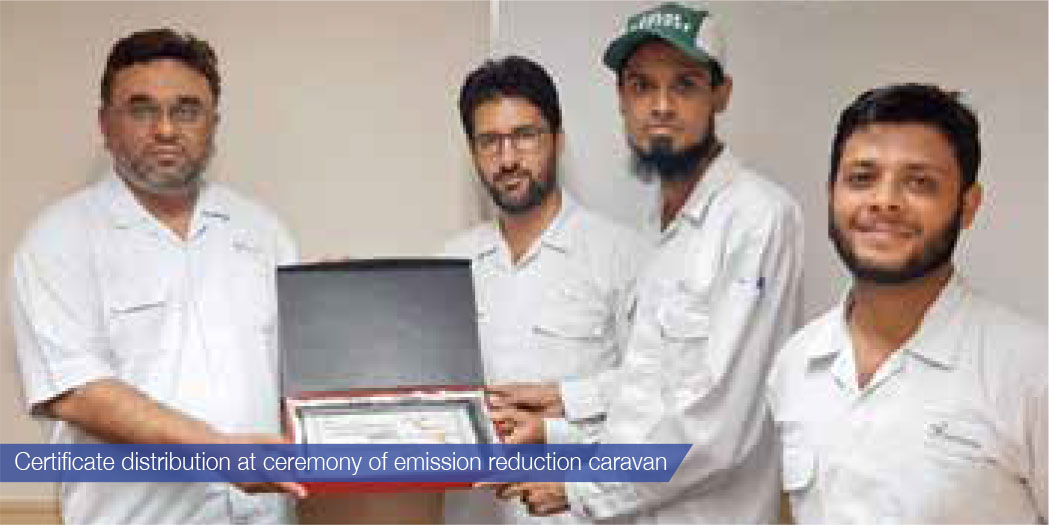
Logistics Operations
The Company’s supply chain operations manage the transportation of parts and components from its vendors to manufacturing facilities (“inbound” freight) while logistics operations ensure the same for finished motorcycles from the Company’s plants to its dealerships (“outbound” freight). With activities coordinated regionally, the responsibilities include designing and operating the transportation network and devising high-quality and efficient packaging to protect materials in transit. Freight emissions are influenced by a wide and complex range of inter-related factors, including the mode of transportation, the efficiency of the equipment used and the design of the freight network. The Company finds the most effective ways of achieving reductions through:
- Improving the design and operation of transportation networks
- Increasing vehicle utilization
- Increasing the use of greener modes of transport such as using rail network
Environmental Impact Assessment Survey
Every year, the Company participates in environmental impact assessment survey developed by Honda Motor Japan. This year, 34 vendors were assessed on basis of following criteria:
- Direct & Indirect GHG Emissions
- Green Purchasing Guideline
- Chemical Substance Management
- Environmental Management System
- Energy Conservation Guidelines
- Water Resources Guidelines
- Pollution Prevention Guidelines
- Biodiversity Guidelines
None of the selected vendors were identified as having any significant actual and potential negative environmental impacts.
Human Rights & Working Conditions
Respecting and protecting human rights – the fundamental and inalienable rights and freedoms to which all people are entitled – is at the core of the Company’s labour practices. The Company aims to ensure that everything it makes or that others make for the Company is consistent with local laws and the Company’s commitment to protecting human rights. The Company has implemented strict requirements within its operations and for suppliers to protect the rights of employees as detailed in following guidelines issued:
- Eliminate discrimination and ensure zero harassment at workplace in any aspect of employment based on race, ethnicity, nationality, religion, gender, or other characteristics;
- Avoid employment of workers who do not meet the legal minimum working age of each country and region;
- Avoid practising forced labour. Guarantee that all labour is voluntary and those employees are free to leave their jobs;
- To comply with the laws & regulations regarding minimum wages, overtime, wage deductions, performance-based pay and other remuneration;
- To obey with the laws & regulations regarding the setting of employees’ working hours (including overtime) and granting of scheduled days off and paid annual vacation time etc.; and
- Ensure a safe and healthy working environment for all associates.
Responsible Sourcing of Minerals
In procurement of certain raw materials, the Company has to comply with Dodd-Frank Act of United States which obligates companies to disclose the origin of certain raw materials to ensure that “conflict minerals”, such as tin, tungsten, tantalum and gold from the Democratic Republic of Congo or neighbouring states, do not enter their products through their supply chain. The Company, therefore, monitors all vendors to make sure they do not source raw materials from the affected regions. Using a structured survey process and by working closely with vendors for increased supply chain transparency, the Company obtains confirmation that its suppliers and their upstream suppliers are obtaining material free from conflict minerals. Furthermore, the Company provides clear guidelines for suppliers and raises awareness on conflict mineral related issues through education and support. The Company also collaborates with a cross-industry group called Conflict-Free Sourcing Initiative (CFSI) in this regard. In order to be confirmed as conflict free, the smelters and refiners are required to pass an independent third-party audit. The results from this year’s survey confirmed that our supply chain is based on conflict free sourcing.
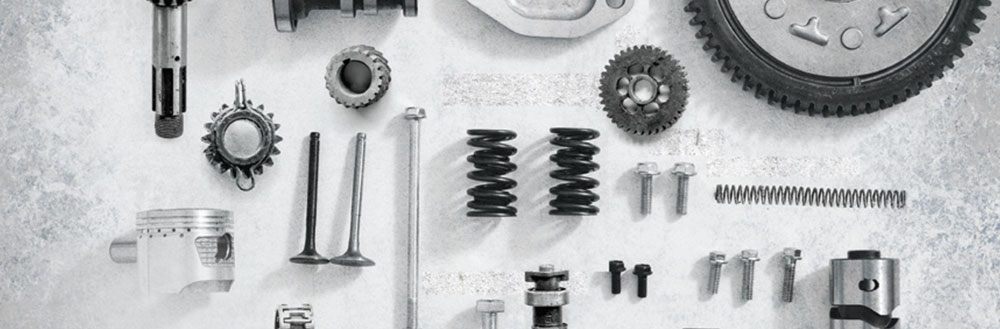
Vendor Management
Management Approach
The Company’s engagement with vendors is a major source of value creation. Therefore, working closely with them on issues, including sustainability is key for achievement of the Company’s long-term goals. The Company’s supply chain has a wide network of vendors and it recognizes the complexity of maintaining sustainability standards within it. At the same time, the Company sees great opportunities in leveraging its expertise and know-how to help vendors improve their performance.
The Company’s supply chain is based on the philosophy of 3As which are:
- Agility: Quick response to any change in demand.
- Alignment: Design strategies aligned with the business plan of company.
- Adaptability: Continuously updated with the latest tools, technologies and methodologies of modern era.
During engagement with vendors, challenges and opportunities are discussed and in-depth analysis is carried out. Solutions to key issues are arrived at mutually. Policies relating to suppliers are evaluated regularly and updated, if required. The Company seeks mutual benefit and carries out business transactions based on principles of unrestricted competition with rational evaluation criteria. The Company’s core focus areas are parts quality, vendor development & environmental and social performance of its vendors.
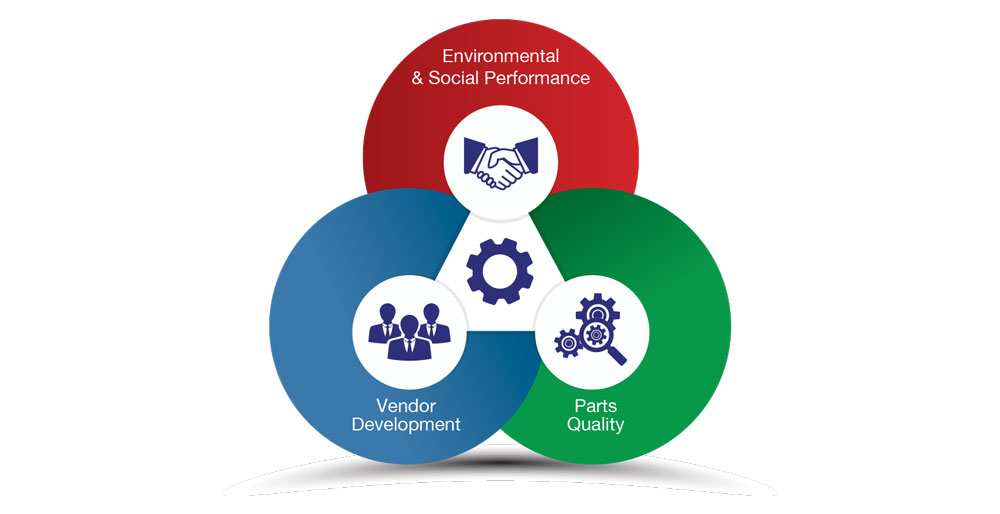
All relevant departments at the Company, including Coordination & Planning, Procurement, Quality Assurance and Logistics are jointly responsible for ensuring sustainable supply chain management. The Company’s focus is on managing and minimizing vendor risks and leveraging vendor potential, in order to ensure sustainability and continuous improvement. A number of company-specific guidelines and policies have been implemented to ensure that the Company and its business partners are aware of local environmental, health, safety, and labour laws, as well as legal requirements and international sustainability principles. These guidelines and policies enable the Company to drive forward the sustainability goals and ensure their compliance.
The Company procures most of its required materials from Pakistan i.e. where its operating facilities are located as far as the same is qualitatively compatible, technically feasible and economically justifiable. The raw materials and parts which are easily available in Pakistan are procured locally, except for those which are not available in Pakistan. However, it is ensured that all materials and parts are strictly aligned with Honda quality standards and are cost effective.
Vendor Induction and Communication
Vendor Selection
The Company’s vendor selection and approval process is based on a criteria comprising not only on their ability to provide quality parts at competitive terms but also their adherence to sustainability principles. Input for sourcing decisions is received from Supply Chain, Production, Coordination & Planning, Logistics and Finance departments. The Company also identifies and works with companies that have standards aligned or consistent with its own procurement and production practices. The Company also ensures that its Vendor Policy and Vendor CSR Guidelines are acknowledged and signed by all of its vendors.
In line with the Company’s selection criteria, all new vendors are screened and inducted only if they comply with sustainability principles detailed in ‘environmental and social performance’ section.
Vendor Diversity
The Company recognizes that a diverse supply base is an integral part of growth and success. It is crucial to deliver the promise of providing the best mobility solutions. The Company is committed to work with and developing businesses by creating opportunities and initiatives that enable diverse vendors to grow into profitable and sustainable enterprises. The Company continues to foster productive relationships with entrepreneurs from a wide range of backgrounds to meet its customers’ needs and expectations.
Business to Business Communication Portal
Open and transparent communication with fair and consistent behaviours is a key component in establishing strong and lasting relationships with the Company’s vendors. The Company has made available various forums for engagement at different levels, including regional vendor meetings, business unit reviews, quarterly business update calls and participation in events organized by vendors and industry associations. In addition, Business to Business link has been established which allows the Company’s supply chain department and vendors to communicate without delays. It has helped to achieve:
- Real Time Communication;
- Paper less Environment;
- On-Time Receiving & delivery; and
- Improvement in efficiency and effectiveness of Supply Chain.
Further, this portal enables evaluation and appraisal of vendors on the basis of standardized quality and timely deliveries.
Parts Quality
The Company aims to keep its customers’ trust by emphasizing on importance of quality throughout its supply chain. To achieve this objective, the Company binds its vendors to establish and operate within a quality assurance system. Apart from the Company’s objective of procuring inspection free parts, its vendors validate that parts delivered through their manufacturing processes meet the drawings accurately and achieve target of 0.1% rejection for incoming parts. Following measures were taken to achieve these quality objectives:
Vendor Improvement Program (VIP)
The Company assists its vendors in improving quality and operations through various initiatives especially the Company’s VIP program launched few years ago. This program focuses on following six core areas:
- Drawing & Specification Control
- Dies & Tool Management
- In Process Inspection System
- Incoming Inspection
- Final Inspection System
- Warranty Analysis system
Certificates are awarded to vendors at the time of completion of the program. Further, they are reviewed and audited each year for recertification. Continuous follow up is carried out by VIP designated team which comprises of the Company’s employees from Supply Chain and Quality Assurance department. This year, 10 more vendors were analyzed and assessed under this program.
ALA Mayar Quality Event
ALA MAYAR Quality Event is an initiative where the Company’s vendors are encouraged to participate and collaborate to solve problems, add value and introduce innovation. Circles are formed where the Company’s employees and those of its vendors work together to discuss issues and devise solutions. This year, more than 150 themes were presented by the Company’s vendors out of which three best themes each from Karachi & Sheikhupura plants were awarded on basis of a pre-defined criteria. The 29th ALA MAYAR Awards were distributed at our Annual Vendor Conference 2019 held on April 29, 2019.
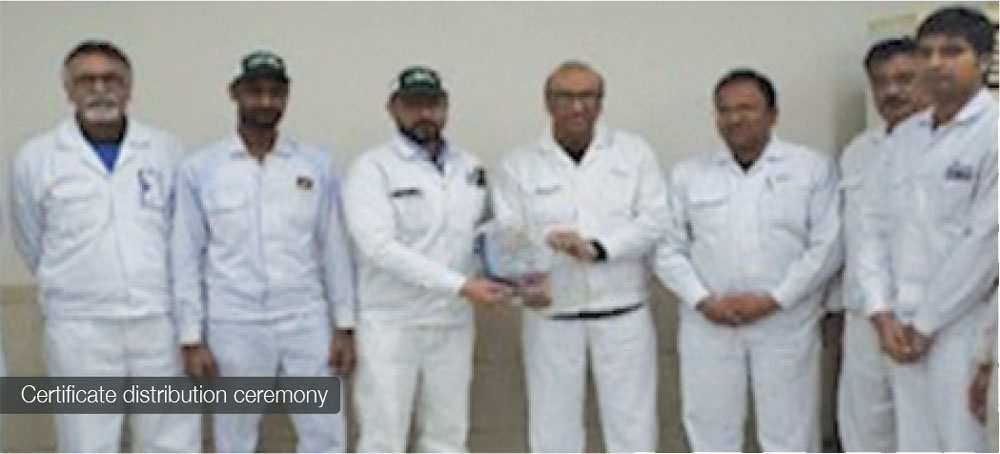
Vendor Development
The Company encourages its vendors to invest in their facilities including enhancing their manufacturing capacity and adapting new technology. The idea is to ensure that the Company’s vendors remain well-equipped to meet the demands of business while earning attractive returns on their investments.
The Company also believes in developing and strengthening competencies and skills of its vendors apart from their manufacturing capacities. For the purpose, the Company has been providing major technological assistance to its vendors, resulting in enhancement of their engineering skills and creation of employment opportunities.
Environmental and Social Performance
The Company applies the same level of scrutiny to its suppliers with regards to labor rights, human rights, and health, social and environmental requirements as it does to its own operations. The Company’s goal is to follow best practices and enable its vendors to replicate the same and be accountable for their sustainability performance.
Guidelines to Vendors
Corporate Social Responsibility is embedded in the Company’s day to day operations in a clear and practical manner. All products and services are regularly monitored for their impact on society and the environment. Given the increased expectations regarding sustainability, the Company recognizes that it is essential to share its approach to sustainability with its vendors. In this regard, following guidelines have been issued to vendors. The Company believes that these guidelines help its vendors in maintaining a shared understanding of sustainability, to carry out initiatives proactively and to continue growing together.
- Establish and monitor a company-wide social management system;
- Prevent climate change via reducing GHG emissions;
- Optimize packaging and establish efficient logistics operations in order to reduce waste disposal and transport emissions;
- Prevent pollution and contamination of air, water, soil, etc;
- Enforce proper disposal of waste and implement optimum recycling of waste and disposals etc; and
- Compliance with laws and regulations along with commitment to protect human rights.
All vendors are monitored and evaluated against these guidelines and based on such evaluation, the Company has not come across any significant actual or potential negative impact of its supply chain or vendors’ on labour practices, human rights and society requiring termination of relationship.
Emission Reduction Caravan
In 2014, the Company undertook an initiative called ‘Emissions Reduction Caravan’ for its vendors. Since then, under this initiative, the Company’s supply chain associates are working in close coordination with major vendors to reduce their environmental footprint. Technical guidance is being provided for process improvements focused on production efficiency, energy conservation, material recycling, reuse and reduction in CO2 emission. 33 vendors from both plants, covering 75% of total purchases have participated and achieved the target of reduction in CO2 emission by 1%.
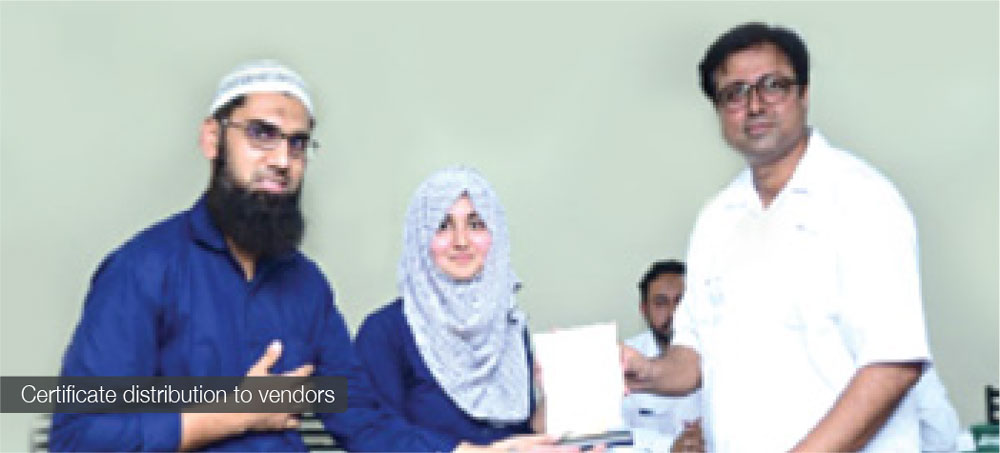
Logistics Operations
The Company’s supply chain operations manage the transportation of parts and components from its vendors to manufacturing facilities (“inbound” freight) while logistics operations ensure the same for finished motorcycles from the Company’s plants to its dealerships (“outbound” freight). With activities coordinated regionally, the responsibilities include designing and operating the transportation network and devising high-quality and efficient packaging to protect materials in transit. Freight emissions are influenced by a wide and complex range of inter-related factors, including the mode of transportation, the efficiency of the equipment used and the design of the freight network. The Company finds the most effective ways of achieving reductions through:
- Improving the design and operation of transportation networks
- Increasing vehicle utilization
- Increasing the use of greener modes of transport such as using rail network
Environmental Impact Assessment Survey
Every year, the Company participates in environmental impact assessment survey developed by Honda Motor Japan. This year, 33 vendors were assessed on basis of following criteria:
- Direct & Indirect GHG Emissions
- Green Purchasing Guideline
- Chemical Substance Management
- Environmental Management System
- Energy Conservation Guidelines
- Water Resources Guidelines
- Pollution Prevention Guidelines
- Biodiversity Guidelines
None of the selected vendors were identified as having any significant actual and potential negative environmental impacts.
Human Rights & Working Conditions
Respecting and protecting human rights – the fundamental and inalienable rights and freedoms to which all people are entitled – is at the core of the Company’s labour practices. The Company aims to ensure that everything it makes or that others make for the Company is consistent with local laws and the Company’s commitment to protecting human rights. The Company has implemented strict requirements within its operations and for suppliers to protect the rights of employees as detailed in following guidelines issued:
- Eliminate discrimination and ensure zero harassment at workplace in any aspect of employment based on race, ethnicity, nationality, religion, gender, or other characteristics;
- Avoid employment of workers who do not meet the legal minimum working age of each country and region;
- Avoid practicing forced labour. Guarantee that all labour is voluntary and those employees are free to leave their jobs;
- To comply with the laws & regulations regarding minimum wages, overtime, wage deductions, performance-based pay and other remuneration;
- To obey with the laws & regulations regarding the setting of employees’ working hours (including overtime) and granting of scheduled days off and paid annual vacation time etc; and
- Ensure a safe and healthy working environment for all associates.
Responsible Sourcing of Minerals
International regulations such as the Dodd-Frank Act in the United States obligate companies to disclose the origin of certain raw materials to ensure that “conflict minerals”, such as tin, tungsten, tantalum and gold from the Democratic Republic of Congo or neighbouring states, do not enter their products through their supply chain. The Company, therefore, monitors all vendors to make sure they do not source raw materials from the affected regions. Using a structured survey process and by working closely with vendors for increased supply chain transparency, the Company obtains confirmation that its suppliers and their upstream suppliers are obtaining material free from conflict minerals. Furthermore, the Company provides clear guidelines for suppliers and raises awareness on conflict mineral related issues through education and support. The Company also collaborates with a cross-industry group called Conflict-Free Sourcing Initiative (CFSI) in this regard. In order to be confirmed as conflict free, the smelters and refiners are required to pass an independent third-party audit. The results from this year’s survey confirmed that our supply chain is based on conflict free sourcing.
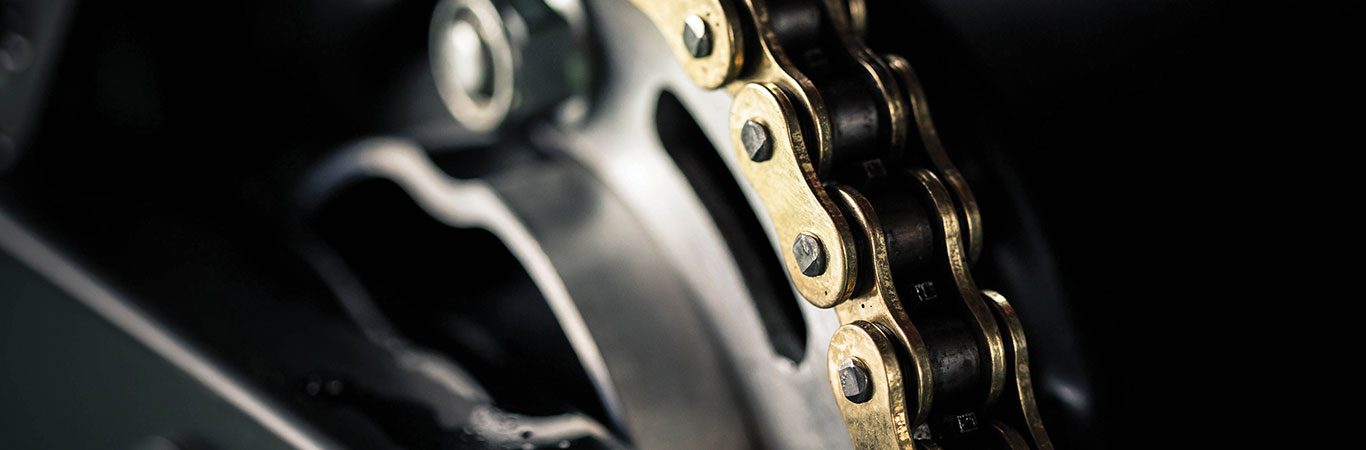
Management Approach
The Company’s engagement with vendors is a major source of value creation. Therefore, working closely with them on issues including sustainability is key for achievement of the Company’s long-term goals. The Company’s supply chain has a wide network of vendors and it recognizes the complexity of maintaining sustainability standards within it. At the same time, the Company sees great opportunities in leveraging its expertise and know-how to help vendors improve their performance.
The Company’s supply chain is based on the philosophy of 3As which are:
- Agility: Quick response to any change in demand.
- Alignment: Design strategies aligned with the business plan of company.
- Adaptability: Continuously updated with the latest tools, technologies and methodologies of modern era.
During engagement with vendors, challenges and opportunities are discussed and in-depth analysis is carried out. Solutions to key issues are arrived at in a collaborative manner. Policies relating to suppliers are evaluated regularly and updated, if required. The Company seeks mutual benefit and carries out business transactions based on principles of unrestricted competition with rational evaluation criteria. The Company’s core focus areas are parts quality, vendor development and environmental and social performance of its vendors.
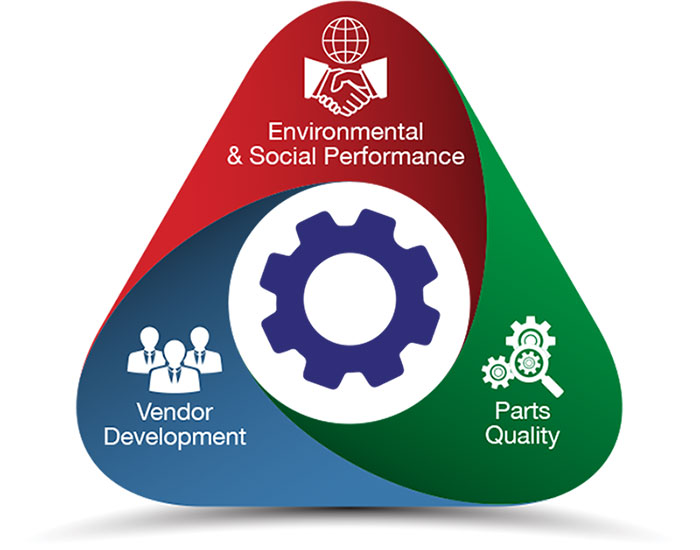
All relevant departments at the Company, including Coordination & Planning, Procurement, Quality Assurance and Logistics are jointly responsible for ensuring sustainable supply chain management. The Company’s focus is on managing and minimizing vendor risks and leveraging vendor potential, in order to ensure sustainability and continuous improvement. A number of company-specific guidelines and policies have been implemented to ensure that the Company and its business partners are aware of local environmental, health, safety, and labor laws, as well as legal requirements and international sustainability principles. These guidelines and policies enable the Company to drive forward the sustainability goals and ensure their compliance.
The Company procures most of its required materials from Pakistan i.e. where its operating facilities are located as far as the same is qualitatively compatible, technically feasible and economically justifiable. The raw materials and parts which are easily available in Pakistan are procured locally, except for those which are not available in Pakistan.
Vendor Induction and Communication
Vendor Selection
The Company’s vendor selection and approval process is based on a criteria comprising not only on their ability to provide quality parts at competitive terms but also their adherence to sustainability principles. Input for sourcing decisions is received from Supply Chain, Production, Coordination & Planning, Logistics and Finance departments. The Company also identifies and works with companies that have standards aligned or consistent with its own procurement and production practices. The Company also ensures that its Vendor Policy and Vendor CSR Guidelines are acknowledged and signed by all of its vendors.
In line with the Company’s selection criteria, all new vendors are screened and inducted only if they comply with sustainability principles detailed in ‘environmental and social performance’ section.
Vendor Diversity
The Company recognizes that a diverse supply base is an integral part of growth and success. It is crucial to deliver the promise of providing the best mobility solutions. The Company is committed to work with and developing businesses by creating opportunities and initiatives that enable diverse vendors to grow into profitable and sustainable enterprises. The Company continues to foster productive relationships with entrepreneurs from a wide range of backgrounds to meet its customers’ needs and expectations.
Business to Business Communication Portal
Open and transparent communication with fair and consistent behaviors is a key component in establishing strong and lasting relationships with the Company’s vendors. The Company has made available various forums for engagement at different levels, including regional vendor meetings, business unit reviews, quarterly business update calls and participation in events organized by vendors and industry associations. In addition, Business to Business link has been established which allows the Company’s supply chain department and vendors to communicate without delays. It has helped to achieve:
- Real Time Communication;
- Paper less Environment;
- On-Time Receiving & delivery; and
- Improvement in efficiency and effectiveness of Supply Chain.
Further, this portal enables evaluation and appraisal of vendors
on the basis of standardized quality and timely deliveries.
Parts Quality
The Company aims to keep its customers’ trust by emphasizing on importance of quality throughout its supply chain. To achieve this objective, the Company binds its vendors to establish and operate within a quality assurance system. Apart from the Company’s objective of procuring inspection free parts, its vendors validate that parts delivered through their manufacturing processes meet the drawings accurately and achieve target of 0.1% rejection for incoming parts. Following measures were taken to achieve these quality objectives:
Vendor Improvement Program (VIP)
The Company assists its vendors in improving quality and operations through various initiatives especially the Company’s VIP program launched few years ago. This program focuses on following six core areas:
- Drawing & Specification Control
- Dies & Tool Management
- In Process Inspection System
- Incoming Inspection
- Final Inspection System
- Warranty Analysis system
Certificates are awarded to vendors at the time of completion of the program. Further, they are reviewed and audited each year for recertification. Continuous follow up is carried out by VIP designated team which comprises of the Company’s employees from Supply Chain and Quality Assurance department. This year, 10 more vendors were analyzed and assessed under this program.
Supplier Quality Management
SQM is an extension of Vendor Improvement Program aimed to reduce vendors’ incoming rejection level. It addresses and emphasizes on supply of high quality parts that satisfy the needs and exceed the expectations of the Company’s customers. This year, 9 suppliers were trained under this program.
ALA MAYAR Quality Event
ALA MAYAR Quality Event is an initiative where the Company’s vendors are encouraged to participate and collaborate to solve problems, add value and introduce innovation. Circles are formed where the Company’s employees and those of its vendors work together to discuss issues and devise solutions. This year, more than 120 themes were presented by the Company’s vendors out of which three best themes each from Karachi & Sheikhupura plants were awarded on basis of a pre-defined criteria. The 28th ALA MAYAR Awards were distributed at our Annual Vendor Conference 2018 held on April 21, 2018.
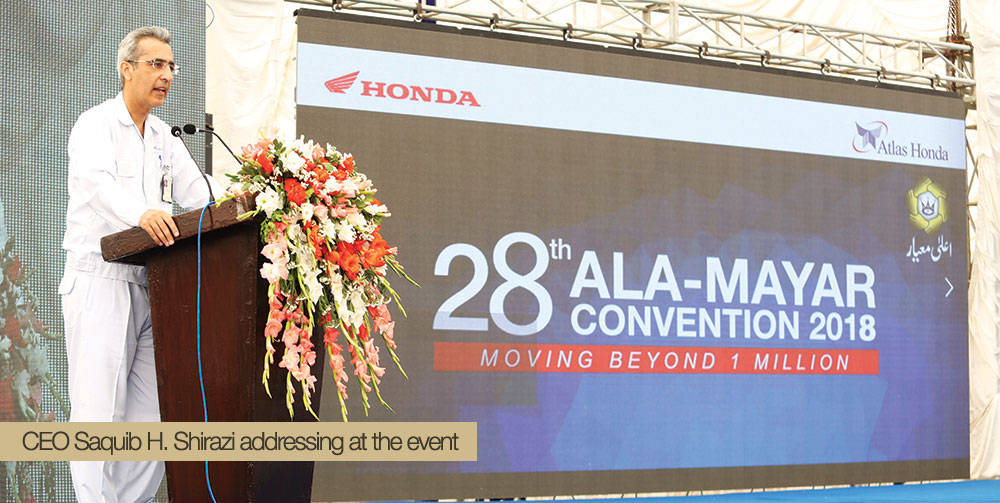
Vendor Development
The Company encourages its vendors to invest in their facilities including their manufacturing capacity and new technology. The idea is to ensure that the Company’s vendors remain well-equipped to meet the demands of business while earning attractive returns on their investments. Since, the Company is going through a phase wise capacity expansion, it is a prerequisite that its vendors upgrade their operations accordingly to support the said expansion. This year, an investment of Rs. 0.3 billion was made by the Company’s vendors in this regard.
The Company also believes in developing and strengthening competencies and skills of its vendors apart from their manufacturing capacities. For the purpose, the Company has been providing major technological assistance to its vendors, resulting in enhancement of their engineering skills and creation of employment opportunities.
Environmental and Social Performance
The Company applies the same level of scrutiny to its suppliers with regards to labor rights, human rights, health, social and environmental requirements as it does to its own operations. The Company’s goal is to follow best practices and enable its vendors to replicate the same and be accountable for their sustainability performance.
Guidelines to Vendors
Corporate Social Responsibility is embedded in the Company’s day to day operations in a clear and practical manner. All products and services are regularly monitored for their impact on society and the environment. Given the increased expectations regarding sustainability, the Company recognizes that it is essential to share its approach to sustainability with its vendors. In this regard, following guidelines have been issued to vendors. The Company believes that these guidelines help its vendors in maintaining a shared understanding of sustainability, to carry out initiatives
proactively and to continue growing together.
- Establish and monitor a company-wide social management system;
- Prevent climate change via reducing GHG emissions;
- Optimize packaging and establish efficient logistics operations in order to reduce waste disposal and transport emissions;
- Prevent pollution and contamination of air, water, soil, etc;
- Enforce proper disposal of waste and implement optimum recycling of waste and disposals etc; and
- Compliance with laws and regulations along with commitment to protect human rights.
All vendors are monitored and evaluated against these guidelines and based on such evaluation, the Company has not come across any significant actual or potential negative impact of its supply chain or vendors’ on labor practices, human rights and society requiring termination of relationship.
Emissions Reduction Caravan
In 2014, the Company undertook an initiative called ‘Emissions Reduction Caravan’ for its vendors. Since then, under this initiative, the Company’s supply chain engineers are working in close coordination with major vendors to reduce their environmental footprint. Technical guidance is being provided for process improvements focused on production efficiency, energy conservation, material recycling, reuse and reduction in CO2 emission. 35 vendors from both plants, covering 76% of total purchases have participated and achieved the target of reduction in CO2 emission by 1%.
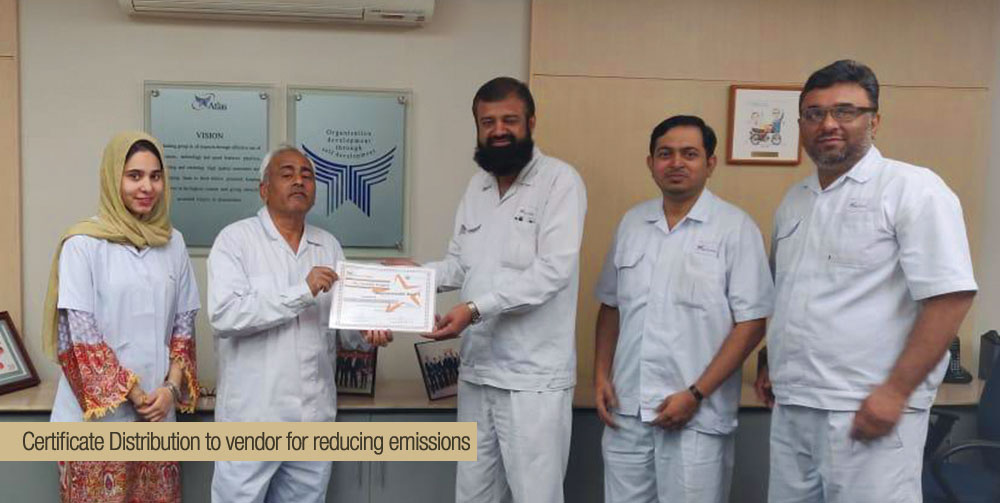
Logistics Operations
The Company’s supply chain operations manage the transportation of parts and components from its vendors to manufacturing facilities (“inbound” freight) while logistics operations ensure the same for finished motorcycles from the Company’s plants to its dealerships (“outbound” freight). With activities coordinated regionally, the responsibilities include designing and operating the transportation network and devising high-quality and efficient packaging to protect materials in transit. Freight emissions are influenced by a wide and complex range of inter-related factors, including the mode of transportation, the efficiency of the equipment used and the design of the freight network. The Company finds the most effective ways of achieving reductions through:
- Improving the design and operation of transportation networks
- Increasing vehicle utilization
- Increasing the use of greener modes of transport such as using rail network
Environmental Impact Assessment Survey
Every year, the Company participates in environmental impact assessment survey developed by Honda Motor Japan. This year, 35 vendors were assessed on basis of following criteria:
- Direct & Indirect GHG Emissions
- Green Purchasing Guideline
- Chemical Substance Management
- Environmental Management System
- Energy Conservation Guidelines
- Water Resources Guidelines
- Pollution Prevention Guidelines
- Biodiversity Guidelines
None of the selected vendors were identified as having any
significant actual and potential negative environmental
impacts.
Human Rights & Working Conditions
Respecting and protecting human rights – the fundamental and inalienable rights and freedoms to which all people are entitled – is at the core of the Company’s labor practices. The Company aims to ensure that everything it makes or that others make for the Company is consistent with local laws and the Company’s commitment to protecting human rights. The Company has implemented strict requirements within its operations and for suppliers to protect the rights of employees as detailed in following guidelines issued:
- Eliminate discrimination and ensure zero harassment at workplace in any aspect of employment based on race, ethnicity, nationality, religion, gender, or other characteristics;
- Avoid employment of workers who do not meet the legal minimum working age of each country and region;
- Avoid practicing forced labor. Guarantee that all labor is voluntary and those employees are free to leave their jobs;
- To comply with the laws & regulations regarding minimum wages, overtime, wage deductions, performance-based pay and other remuneration;
- To obey with the laws & regulations regarding the setting of employees’ working hours (including overtime) and granting of scheduled days off and paid annual vacation time etc; and
- Ensure a safe and healthy working environment for all associates.
Responsible Sourcing of Minerals
International regulations such as the Dodd-Frank Act in the United States obligate companies to disclose the origin of certain raw materials to ensure that “conflict minerals”, such as tin, tungsten, tantalum and gold from the Democratic Republic of Congo or neighboring states, do not enter their products through their supply chain. The Company, therefore, monitors all vendors to make sure they do not source raw materials from the affected regions. Using a structured survey process and by working closely with vendors for increased supply chain transparency, the Company obtains confirmation that its suppliers and their upstream suppliers are obtaining material free from conflict minerals. Furthermore, the Company provides clear guidelines for suppliers and raises awareness on conflict mineral related issues through education and support. The Company also collaborates with a cross-industry group called Conflict-Free Sourcing Initiative (CFSI) in this regard. In order to be confirmed as conflict free, the smelters and refiners are required to pass an independent third-party audit. The results from this year’s survey confirmed that our supply chain is based on conflict free sourcing.
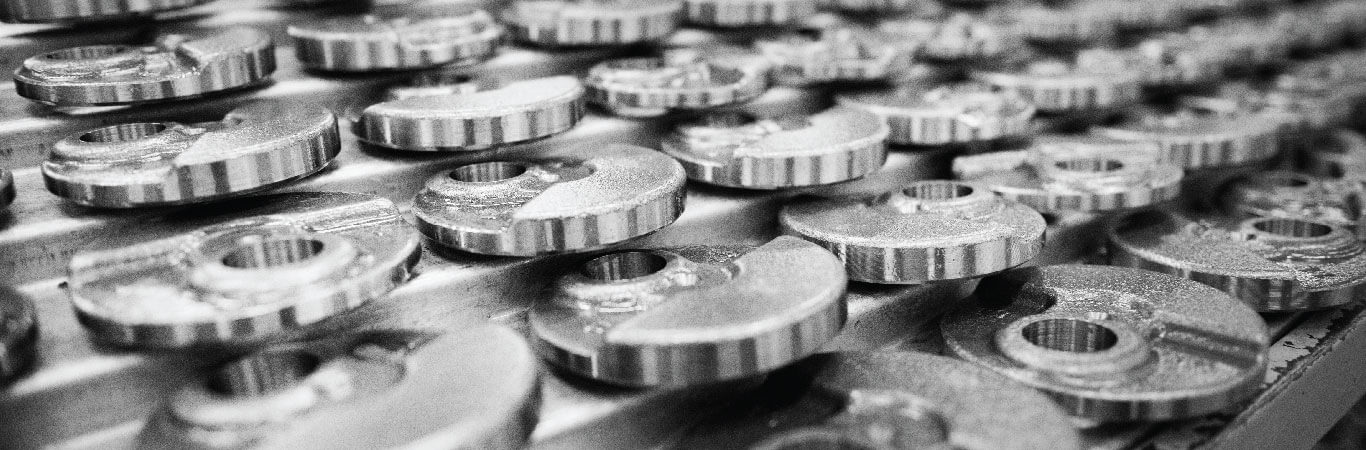
Our Management Approach
Our engagement with our vendors is a major source of value creation. We are convinced that working closely with vendors on issues including sustainability is key to achieve our own long-term goals, underscoring our position as a responsible manufacturer of two-wheelers and delivering an overall premium experience to our customers. Our supply chain has a vast network of vendors and we recognize the complexity of maintaining sustainability standards within it. At the same time, we see great opportunities in leveraging our own expertise and know-how to help vendors
improve their performance.
Our supply chain is based on the philosophy of 3As which are:
- Agility: We can quickly respond to any change in demand.
- Alignment: Our supply chain designs strategies aligned with the business plan of Company.
- Adaptability: We stay updated with the latest tools, technologies and methodologies of modern era.
In our engagement with vendors, we constantly discuss the challenges and opportunities we face and develop in-depth analysis on, and solutions to, key issues in a collaborative manner. Policies relating to our suppliers are evaluated regularly and updated, if required. We seek mutual benefit and carry out business transactions based on principles of unrestricted competition with rational evaluation criteria. Our core focus areas are
parts quality, vendor development and environmental and social performance of our vendors.
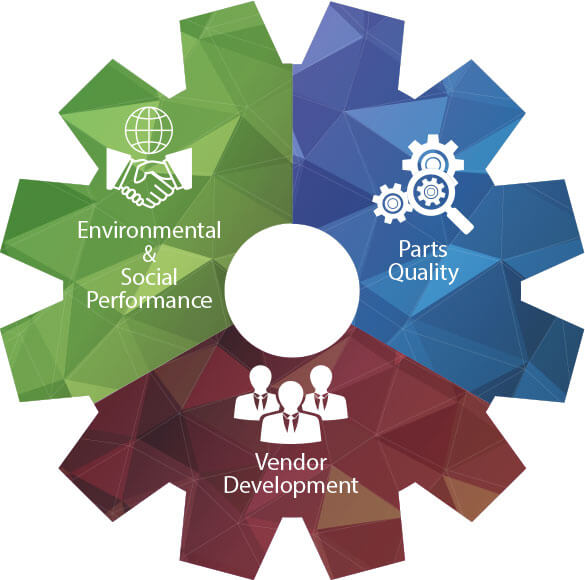
All relevant departments of Atlas Honda, including Research and Development, Procurement, Quality Assurance and Logistics are jointly responsible for ensuring sustainable supply chain management. We focus on managing and minimizing vendor risks and leveraging vendor potential, in order to ensure sustainability and continuous improvement throughout our network. A number of company-specific guidelines, policies and procedures have been implemented to ensure that we and our business partners are aware of local environmental, health, safety, and labour laws, as well as legal requirements and international sustainability principles. These guidelines and policies enable us to drive forward the sustainability goals of
our supply chain and ensure their compliance.
Vendor Induction and Communication
Vendor Selection
Our vendor selection and approval process is based on a criteria comprising not only on their ability to provide quality parts at competitive terms but also their adherence to sustainability principles. We gain input for sourcing decisions from Supply Chain, Production, Commercial, Logistics and Finance departments. We also seek to identify and work with companies having standards that are aligned or consistent with our procurement and production practices. We ensure that our ‘Vendor Policy’ and ‘Vendor CSR Guidelines’ are acknowledged and signed
by all of our vendors.
We procure most of our requirements from locations in which our respective operating facilities are located as far as the same is qualitatively compatible, technically feasible, and economically justifiable. The raw materials and other components which are easily available in Pakistan are procured locally, except for those that are not available in Pakistan.
Vendor Diversity
We recognize that a diverse supply base is an integral part of our growth and success. It is crucial to deliver our promise of providing the best mobility solutions. We are committed to work with and develop businesses by creating opportunities and initiatives that enable diverse vendors to grow into profitable and sustainable enterprises. We continue to foster productive relationships with entrepreneurs from a wide range of backgrounds to meet our customers’ needs and expectations.
Business to Business Communication Portal
Open and transparent communication with fair and consistent behaviours is a key component in establishing strong and lasting relationships with our vendors. We have made available various forums for engagement at all levels, including regional vendor meetings, business unit reviews, quarterly business update calls and participation in events organized by vendor and industry associations. In addition, Business to Business link has been established which allows our supply chain department and vendors to communicate without delays. It has helped us achieve:
- Real Time Communication.
- Paper less Environment.
- On-Time Receiving & delivery
- Improvement in efficiency and effectiveness of Supply Chain.
Further, this portal enables us to evaluate and appraise our vendors on the basis of standardized quality and timely deliveries.
Part Quality
We aim to keep our customers’ trust by emphasizing on importance of quality throughout our supply chain. To achieve this objective, we bind our vendors to establish and operate within a quality assurance system. Apart from our vision to procure inspection free parts, our vendors validate that parts delivered through their manufacturing processes meet our drawings accurately and achieve target of 0.1% rejection for incoming parts. Following measures were taken to achieve these quality objectives:
Vendor Improvement Program (VIP)
We launched our VIP program few years ago to improve quality and operations of our vendors. This program focuses on following six core areas:
- Drawing & Specification Control
- Dies & Tool Management
- In Process Inspection System
- Incoming Inspection
- Final Inspection System
- Warranty Analysis system
Certificates are awarded to vendors at the time of completion of the program. Further, they are reviewed and audited each year for recertification. Continuous follow up is made by VIP designated team which comprises of our employees from supply chain and quality department. This year, 18 more vendors were analyzed and assessed under this program.
Supplier Quality Management
SQM is an extension of VIP aimed to achieve the goal of 0.1% rejection level. It addresses and emphasizes on supply of high quality parts that satisfy the needs and exceed the expectations of our customers. This year, 30 suppliers were trained under this program.
AALA Mayar Quality Event
AALA MAYAR Quality Event is our initiative where our vendors are encouraged to participate and collaborate with us to solve problems, add value and introduce innovation. Circles are formed where our employees and vendors work together to discuss issues and devise solutions. This year, more than 100 themes were presented by our vendors in this context out of which three best themes each from Karachi & Sheikhupura plants were awarded on the basis of a pre-defined criteria. The 27th AALA MAYAR Awards were distributed at our Annual Vendor Conference 2017 held on May 22, 2017.
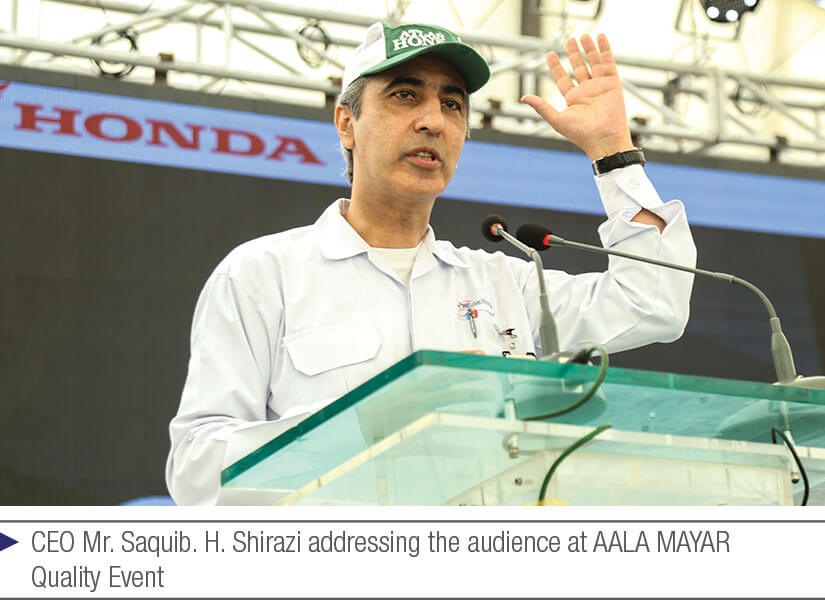
Vendor Development
We encourage our vendors to invest in their facilities including their manufacturing capacity and new technology. The idea is to ensure that our vendors remain well-equipped to meet the demands of our business while earning attractive returns on their investments. Since, we are under-going a phase wise capacity expansion, it is a prerequisite that our vendors upgrade their operations accordingly to support the said expansion. This year, an investment of Rs. 0.7 billion was made by our vendors in this regard.
We also believe in developing and strengthening competencies and skills of our vendor apart from their manufacturing capacities. For the purpose, we have been providing major technological assistance to our vendors, resulting in enhancement of their engineering skills and creation of employment opportunities.
Environmental and Social Performance
We are committed to continuously manage environmental and social impacts with responsibility within our supply chain, as well as our own operations. Our goal is to follow the best practices and enable our vendors to replicate the same and be accountable for their sustainability performance.
Guidelines to Vendors
Corporate Social Responsibility is embedded in our routine operational management in a clear and practical manner. All our products and services are regularly monitored for their impact on society and the environment. Given the increased expectations regarding sustainability, we recognize that it is essential to share our approach to sustainability with our vendors. In this regard, following guidelines have been issued to the vendors. We believe that these guidelines help our vendors in maintaining a shared understanding of sustainability, to carry out initiatives proactively and to continue growing together as companies that society wants to exist.
- Establish and monitor a company-wide social management system.
- Prevent climate change via reducing GHG emissions.
- Optimize packaging and establish efficient logistics operations in order to reduce waste disposal and transport emissions.
- Prevent pollution and contamination of air, water, soil, etc.
- Enforce proper disposal of waste and implement optimum recycling of waste and disposals etc.
- Compliance with laws and regulations along with commitment to protect human rights.
All vendors are monitored and evaluated against these guidelines and based on such evaluation, we have not come across any significant actual or
potential negative impact of our supply chain or vendors on labour practices, human rights and society requiring termination of relationship.
Emission Reduction Caravan
In 2014, we undertook an initiative called ‘Emissions Reduction Caravan’ for our vendors. Since then, under this initiative, our supply chain engineers are working in close coordination with major vendors to reduce their environmental footprint. Technical guidance is being provided for process improvements focused on production efficiency, energy conservation, material recycling, reuse and reduction in CO2 emission. 35 vendors from both plants, covering 78% of total purchases have participated and achieved the target of reduction in CO2 emission by 1%.
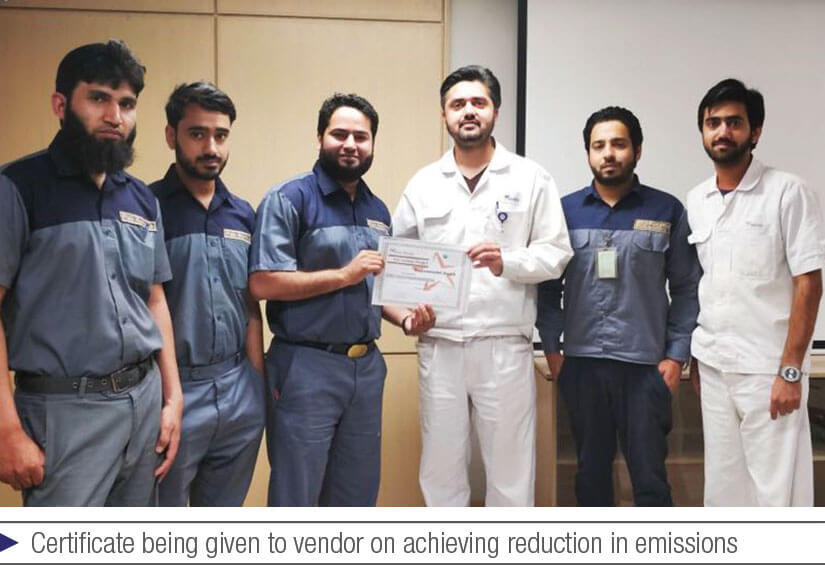
Logistics Operations
Our supply chain operations manage the transportation of parts and components from our vendors to our manufacturing facilities (“inbound” freight) while logistics operations ensure the same for our finished motorcycles from our plants to our dealerships (“outbound” freight).
With activities coordinated regionally, the responsibilities include designing and operating the transportation network and devising high-quality and efficient packaging to protect materials in transit. Freight emissions are influenced by a wide and complex range of inter-related factors, including the mode of transportation, the efficiency of the equipment used and the design of the freight network. We find the most effective ways of achieving reductions are through:
- Improving the design and operation of our transportation networks
- Increasing vehicle utilization
- Increasing the use of greener modes of transport, such as rail and water
Environmental Impact Assessment Survey
Every year, we participate in environmental impact assessment survey developed by Honda Motor Japan. This year, 35 vendors were assessed on the basis of following criteria:
- Direct & Indirect GHG Emission
- Green Purchasing Guideline
- Chemical Substance Management
- Environmental Management System
- Energy Conservation Guidelines
- Water Resources Guidelines
- Pollution Prevention Guidelines
- Biodiversity Guidelines
None of the selected vendors were identified as having any significant actual and potential negative environmental impacts
Human Rights & Working Conditions
Our human rights and working conditions program is an integral part of our efforts to develop a more sustainable and ethical supply chain. We aim to ensure that everything we make – or that others make for us – is consistent with local laws and our commitment to protecting human rights. Following guidelines are issued to our vendors for addressing human rights and working conditions related concerns:
- Eliminate discrimination in any aspect of employment based on race, ethnicity, nationality, religion, gender, or other characteristics.
- Ensure zero harassment in the workplace on the basis of race, ethnicity, and nationality of birth, religion, gender, or other characteristics.
- Avoid employment of workers who do not meet the legal minimum working age of each country and region.
- Avoid practicing forced labour. Guarantee that all labour is voluntary and that employees are free to leave their jobs.
- To comply with the laws & regulations regarding minimum wages, overtime, wage deductions, performance-based pay and other remuneration
- To obey with the laws & regulations regarding the setting of employees’ working hours (including overtime) and the granting of scheduled days off and paid annual vacation time etc.
- Ensure a safe and healthy working environment for all associates.
Approach to Conflict Minerals
International regulations such as the Dodd-Frank Act in the United States obligate companies to disclose the origin of certain raw materials to ensure that “conflict minerals”, such as tin, tungsten, tantalum and gold from the Democratic Republic of Congo or neighboring states, do not enter their products through their supply chain. We, therefore, monitor all vendors to make sure they do not source raw materials from the affected regions. Using a structured survey process and by working closely with our vendors for increased supply chain transparency, we obtain confirmation that our suppliers and their upstream suppliers are obtaining material free from conflict minerals. We also collaborate with a cross-industry group called Conflict-Free Sourcing Initiative (CFSI) in this regard. In order to be confirmed as conflict free, the smelters
and refiners are required to pass an independent third-party audit. The results from this year’s survey confirmed that our supply chain is based on conflict free sourcing.
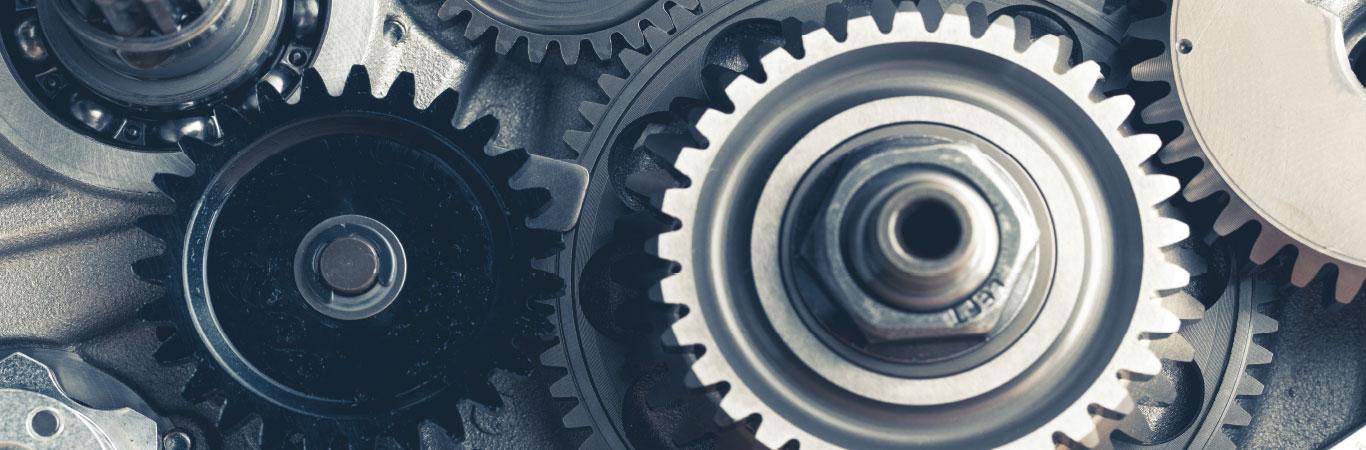
Management Approach
AHL is aware that long term success cannot be achieved without reliable business partners. The business process integration involves collaborative work between buyer and vendors, joint product development and shared continuous information flow which in turn assist to achieve the best product flows. Our approach to supply chain management is supported by our strategic, tactical and operational framework and decisions. Our core focus areas are parts quality, vendor development and environmental and social performance of our vendors.
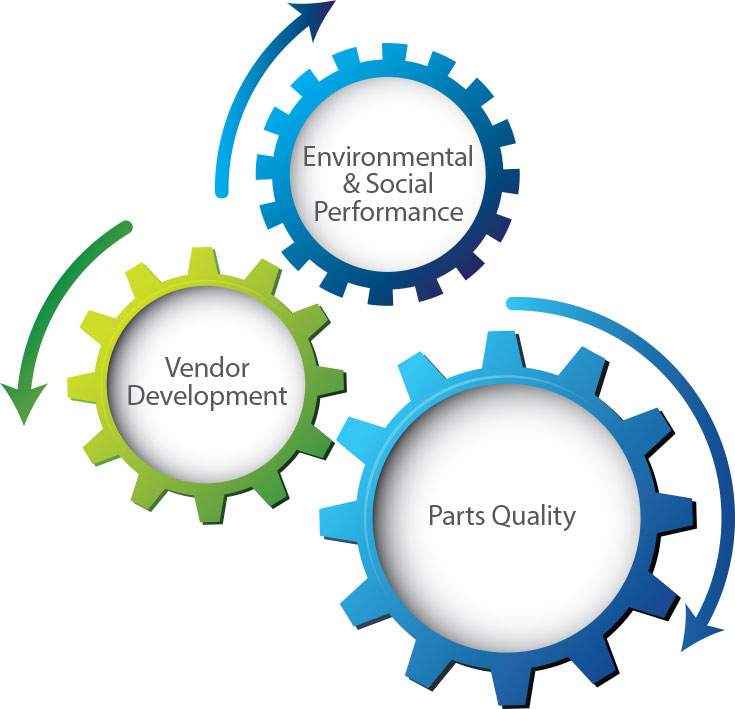
AHL aims to build transparent and reliable relationships with our vendors and manage procurement in an open manner, while sharing objectives from a long-term and global perspective. AHL carries out transactions under the principle of free competition with rational evaluation criteria, and seeks mutual benefit with vendors. Having a global outlook, the Company carries out procurement in the regions that best suit its operational needs.
Vendor development is another important tenet of the Company’s supply chain philosophy. It prefers to build where it sells and to buy where it builds. This enables its products to be more competitive because these are built to suit unique local requirements and conditions that drive customer enthusiasm and brand loyalty.
Further, we aim to expand the scale of our product life cycle analysis to better understand where our greatest environmental impacts occur in the supply chain and to evaluate monitoring tools and engagement opportunities to strengthen our supplier relationships around sustainability efforts.
Our supply chain is based on the philosophy of 3A’s of supply chain which are:
- Agility: We can quickly respond to any change in demand.
- Alignment: Our supply chain designs its strategies aligned with the Business Plan of the Company.
- Adoptability: We try to keep updated with the latest tools, technologies and methodologies of modern era.
Vendor Screening & Communication
Selecting and Screening Vendors
AHL select and approve vendors based upon their ability to provide quality parts, technology and innovation on a competitive basis. We gain input for sourcing decisions not only from Supply Chain departments but also from Production, Commercial, Logistics, and Finance. We also seek to identify and work with companies that have standards that are aligned or consistent with our Procurement and Production Practices. AHL is committed to ensure that its supply chain respect labor rights, human rights and engage in productive practices for society. AHL is not aware of any significant actual or potential negative impacts of its operations or suppliers on labor practices, human rights and society. Moreover, AHL is also not aware of any cases where AHL or its suppliers have instance of child labor and forced or compulsory labor.
Vendor Diversity
AHL recognize that a diverse supply base is an integral part of our overall growth and success, providing fresh perspectives that lead to cutting-edge innovations and accelerated business development. Having a diverse supply base is crucial to deliver our promise to help the world move well. We are committed to work with and develop vendors by creating business opportunities and initiatives that enable diverse vendors to grow into profitable and sustainable enterprises. We continue to foster productive relationships with entrepreneurs from a wide range of backgrounds to meet our customers’ needs and expectations.
CSR Guideline to Vendors
Given the mounting social expectations towards CSR activities, we believe it is essential to share “Honda’s approach to CSR” with our vendors, who are key Honda business partners, and to work together as one team to promote CSR initiatives. Towards this end, Honda published the “Vendor CSR Guidelines.” We expect that these Guidelines will help our vendors in maintaining a shared understanding of CSR, to carry out CSR initiatives proactively, and to continue growing together as companies that society wants to exist.
Business to Business Communication Portal
The open, honest and transparent communication with fair, honorable and consistent behaviors is a key component in establishing strong, lasting relationships with our vendors. AHL has established several forums for engagement at all levels of the organization, including regional vendor meetings, business unit reviews, quarterly business update calls, and participation in vendor and industry association events.
Additionally, Business to Business link has been established between AHL and its vendors in the span of continuous improvement. By this exertion, AHL Supply Chain and its vendors work together to mutually promote business environment improvements and it is aimed at maximizing customer satisfaction. It leads us to achieve:
- Real Time Communication.
- Paper less Environment.
- On-Time Receiving & delivery
- Improvement in efficiency and effectiveness of Supply Chain.
One the other hand, this portal enables us to evaluate and appraise our vendors on the basis of standardized quality, timely deliveries, cost competitiveness and financial reliability.
Part Quality
AHL aims to keep its customers’ trust by emphasizing importance of quality throughout its supply chain. To achieve this objective, we bind our vendors to establish and operate a company-wide quality assurance system. Apart from our vision to procure inspection free parts, our vendors validate that their manufacturing processes deliver us parts that meet our drawings accurately and achieve 0.1% rejection target for incoming parts. During the year, following activities were carried out to achieve quality objectives:
Vendor Improvement Program (VIP)
AHL launched VIP program few years ago to improve quality and operations at the vendor end. This program focuses on following six core areas:
- Drawing & Specification Control
- Dies & Tool Management
- In Process Inspection System
- Incoming Inspection
- Final Inspection System
- Warranty Analysis System
Vendors selected under this program are gone through series of checks and reviews. Certificates are awarded at the end of VIP program and vendors are reviewed and audited each year for recertification. Continuous follow up is made by VIP designated team which is comprised of supply chain and quality department associates. During the year, 18 vendors were analyzed and assessed under vendor improvement program.
AALA MAYAR Quality Event
AALA MAYAR Quality Event is a participatory management technique that enlists the involvement of employees and vendors in solving problems, value addition and introducing innovation related to their own jobs. Circles are formed for both AHL and vendor’s employees working together in an operation who meet at intervals to discuss problems of quality and to devise solutions for improvements.
Last year 26th AALA MAYAR awards were distributed on 24th March 2016 at AHL Annual Vendor Conference 2016, where all of AHL’s vendors participated. Around 108 themes were presented by vendors in the context of improvement in the areas of quality and manufacturing innovations. Three best themes each from Karachi & Shaikhupura plants were awarded on the basis of pre-defined criteria.
Supplier Quality Management (SQM)
To further proceed to achieve the goal of 0.1% rejection level, SQM is the extension of Vendor Improvement Program. It addresses and emphasizes on to establish a process of providing high quality that satisfies and exceeds the expectations of Honda product users. During the year, 30 vendors were trained under this program.
Vendor Development
Capacity Expansion
Focusing on the Business Enhancement and Expansion, AHL Supply chain encourages its vendors to invest in its manufacturing capacities, facilities and modern technology. The objectives of these investments are to support the increase in AHL market share and a good and attractive return on vendor’s investment.
In our Capacity Expansion Inauguration Ceremony held on October 20, 2016 at Sheikhupura Plant graced by participations of Mr. Takahiro Hachigo President & CEO and other top officials of Honda Motor Company. A total of 135 vendors from all over Pakistan participated in the event where numerous vendors were awarded for standing along with AHL to achieve desired expansion targets. This year, an investment of Rupees 0.61 billion was made by vendors in the purchasing and up gradation of their plants, machines and accessories for capacity expansion.
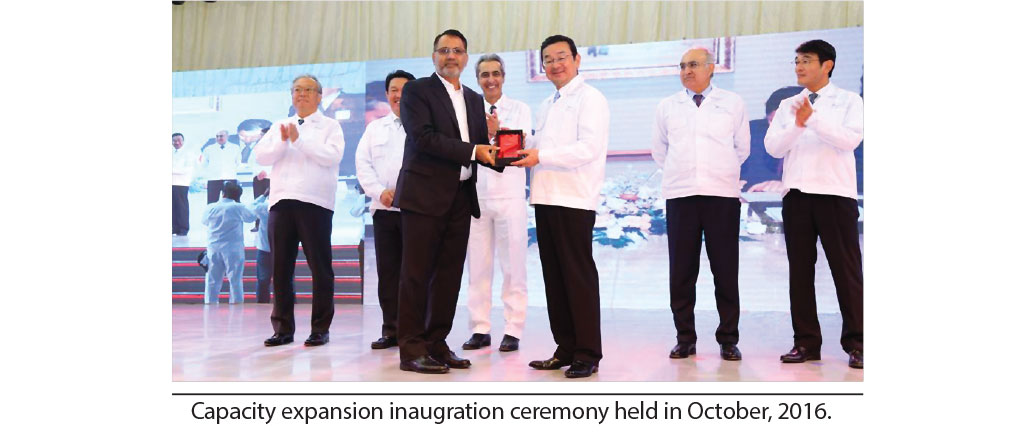
Localization
The Company believes in developing and strengthening vendor’s competencies along with manufacturing capacities. For the purpose, the Company played a major role in providing technological and financial assistance, resulting in enhancement of engineering skills and creation of thousands of job. The Company continues to support the vendors in every possible way and conducted various programs for improving their quality and capacity.
Goshi Thang Long Auto Parts Co. Ltd. (Vietnam) Plant Visit
Our six vendors involved in manufacturing for Steel Metal & Chrome plating parts visited Goshi Thang Long Auto Parts Co. Ltd. (Vietnam) Plant. During their visit, they had the opportunity for developing good understanding of high quality manufacturing processes, plating operations and increasing their efficiency and effectiveness.
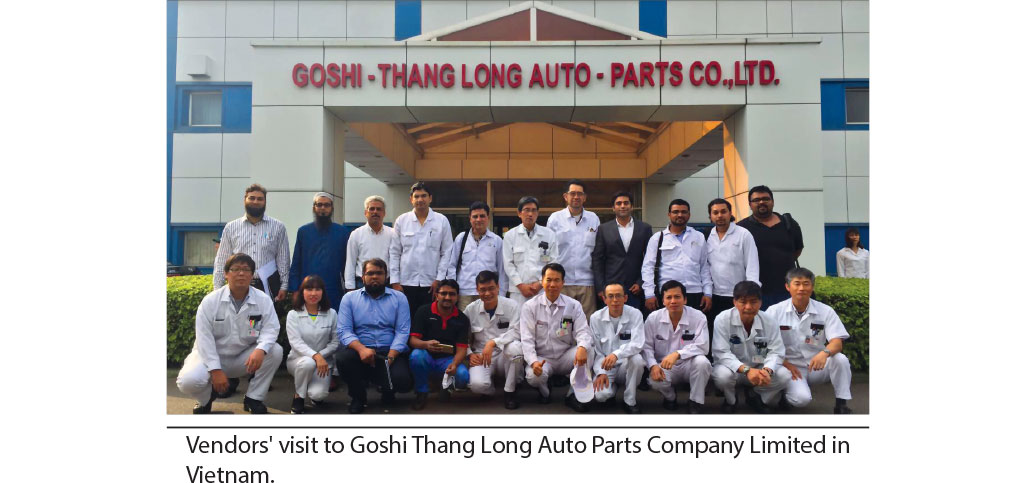
Environmental and Social Performance
AHL is committed to reduce the environmental footprint of our supply chain, as well as our vehicles and our operations while encouraging social performance at the vendor end. Our goal is to share leading energy, GHG emission, water reduction initiatives and human right practices implemented in our own manufacturing plants, enabling vendors to replicate best practice, minimize their impacts on the environment and society and to be accountable for their sustainability performance.
Guidelines to Vendors
To ensure Environmental & Social Performance at vendor end, following guidelines are issued to vendors:
- Establish and monitor a company-wide environmental management system.
- Prevent climate change via reducing greenhouse gas emissions.
- Optimize packaging and establish efficient logistics operations in order to reduce waste disposal and transport emissions.
- Prevent pollution and contamination of air, water, soil, etc.
- Enforce proper disposal of waste and implement optimum recycling of waste and disposals etc.
- Compliance with laws and regulations along with commitment to protect human rights.
Emission Reduction Caravan
From 2014 onwards, the Company undertook a vendor initiative in the area CO2 emissions reduction control, ‘Emissions Reduction Caravan’ at Atlas Honda Limited. The Company believes in The Three Realities Principle – of which the first step is “going to the actual place.” In this spirit, the Supply Chain engineers are working in close coordination with major vendors and vendors to control their environmental footprint. The Company’s engineers provide technical guidance to vendors for process improvements focusing on production efficiency, energy conservation, material recycling and reuse and reduction in CO2 emission.
In total 38 vendors from both plants, covering 76% of total purchasing amount participated in Emission Reduction Caravan. The target was to reduce 1% CO2 Emission by each vendor. Resultantly, the reduction has successfully been achieved in direct emission of burning of fossil fuels, indirect emission of purchased electricity, purchased goods and transportation respectively.
Optimizing Packaging
Material Management Department focuses on designing, procuring and optimizing packaging to best suit the items being moved and the transport mode involved. Packaging has environmental impacts throughout its life cycle, including material use, transport emissions and waste disposal. The Company’s experiences over time have confirmed to us that the best strategy for eliminating waste and optimizing efficiency is to use durable, returnable packaging. This generally means the development of robust plastic containers that can survive years of repeated re-use.
AHL’s standard range of packaging not only protects its contents but also allows maximum storage density during transportation. Packaging of new parts before the full-volume launch of any product is reviewed, to assess any improvement opportunities.
Logistics Operations
Our supply chain operations manage the safe and efficient transport of parts and components from our vendors to our manufacturing plants (“inbound” freight), and our logistics operations ensure the same for finished vehicles from our plants to our dealerships (“outbound” freight). With activities coordinated regionally, its responsibilities include designing and operating our transportation networks, and devising high-quality and efficient packaging to protect materials in transit.
The freight emissions are influenced by a wide and complex range of inter-related factors, including the mode of transport, the efficiency of the equipment used and the design of the freight network. We find the most effective ways of achieving reductions are through:
- Improving the design and operation of our transportation networks
- Increasing vehicle utilization
- Increasing the use of greener modes of transport, such as rail and water
Environmental Impact Assessment Survey
The Company participated in environmental impact assessment survey developed by Honda Motors Japan. 38 vendors were surveyed for environmental assessment on following grounds and resultantly none of the selected vendors were identified as having significant actual and potential negative environmental impacts. The vendors were evaluated on the basis of following criteria:
- Direct & Indirect GHG Emission
- Green Purchasing Guideline
- Chemical Substance Management
- Environmental Management System
- Energy Conservation Guidelines
- Water Resources Guidelines
- Pollution Prevention Guidelines
- Biodiversity Guidelines
3rd ATAI Environmental Conference 2016
Atlas Honda took part in the ATAI environmental conference 2016 which was held in the mid of May 2016 in Bangkok, Thailand. Honda’s Joint ventures and its subsidiaries from the ASIA OCEANA region, comprises of eight countries and 17 companies participated in this conference. The representatives presented the CO2 Emission Reduction Activities that were conducted on their selected vendors. The CO2 emission reduction target was 1% per year and on an average all the selected vendors achieved it successfully.
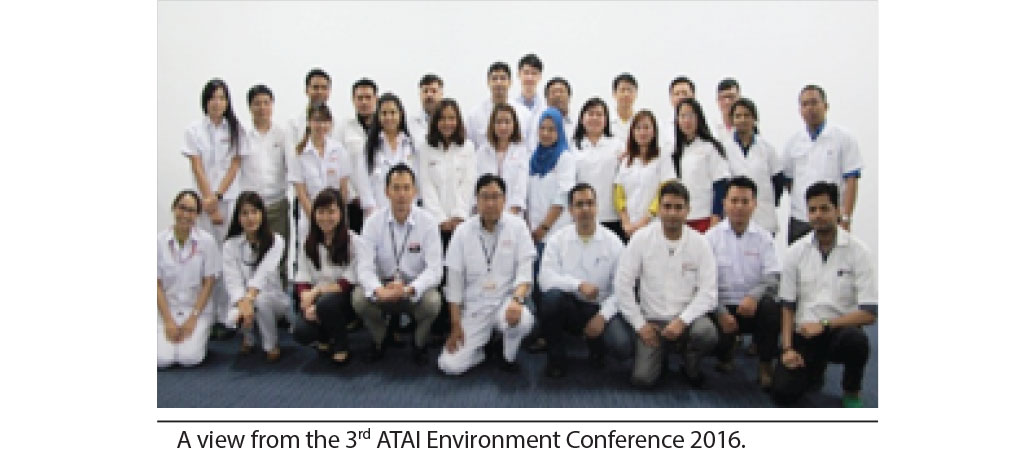
Human Rights and Working Conditions
AHL is committed to respecting human rights everywhere we operate. Our human rights and working conditions program is an integral part of our efforts to develop a more sustainable and ethical supply chain. We aim to ensure that everything we make – or that others make for us – is consistent with local law and our own commitment to protecting human rights. Following guidelines are issued to our vendors for addressing human rights and working conditions related concerns:
- Eliminate discrimination in any aspect of employment based on race, ethnicity, nationality, religion, gender, or other characteristics.
- Ensure zero harassment in the workplace on the basis of race, ethnicity, and nationality of birth, religion, gender, or other characteristics.
- Avoid employment of child labor who does not meet the legal minimum working age of each country and region.
- Avoid practicing forced labor. Guarantee that all labor is voluntary and that employees are free to leave their jobs.
- Comply with the laws & regulations regarding minimum wages, overtime, wage deductions, performance-based pay and other remuneration.
- Comply with the laws & regulations regarding the setting of employees’ working hours (including overtime) and the granting of scheduled days off and paid annual vacation time etc.
- Ensure a safe and healthy working environment for all associates. This is our priority and we aim to prevent any accident or injury.
Conflict Minerals Background
On August 22, 2012, the U.S. Securities and Exchange Commission (SEC) adopted the final rule to implement reporting and disclosure requirements concerning conflict minerals, as directed by Section 1502 of the Dodd-Frank Wall Street Reform and Consumer Protection Act of 2010. The congressional mandate was designed to further the humanitarian goal of ending violent conflict in the Democratic Republic of the Congo (DRC) and adjoining countries.
AHL Approach Towards Conflict Minerals
Our approach to managing conflict minerals compliance is consistent with our supply chain sustainability approach, and we are working closely with our vendors to increase supply chain transparency. We are many layers removed from the smelters and refiners in our supply base, therefore, we must survey our direct vendors and request our vendors, in turn, to survey their vendors until the point many layers down in the supply chain where the smelters or refiners of the 3TG (tantalum, tin, tungsten, and gold) are known. Once the smelters or refiner are identified and reported to us, we then work with a cross-industry group called Conflict-Free Sourcing Initiative (CFSI) to determine if the smelters reported by our supply chain have been confirmed to be conflict free. In order to be confirmed as conflict free, the smelters and refiners must pass an independent third-party audit.
The results from this year’s survey confirmed that our Supply chain is based on Conflict Free Sourcing with no black vendors.